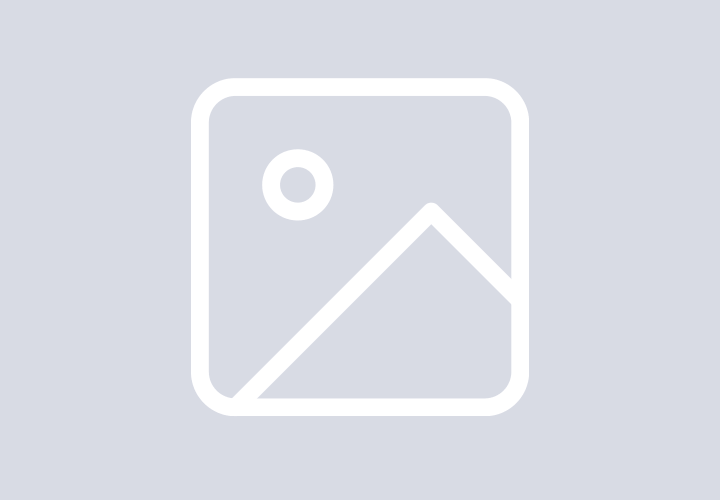
Helicopter dynamic components
Helicopter dynamic components
KONGSBERG performs services on key dynamic helicopter components: main, tail and intermediate gear boxes, main and tail rotor heads and drive shafts.
Main phases
- Receiving inspection
- Technical documentation issue
- Disassembly
- Inspection
- Reassembly
- Test bench run
- Inspection after the green run
- Oil leak test and preservation
- Painting
- Issue of acceptance documentation (statement of maintenance conformity)
- Delivery
KONGSBERG carries out work on the following components for Sea King, AW101 and NH-90: Main Gear Box, Main Rotor Head, Accessory Gearbox, Intermediate Gear Box, Tail Gear Box, Tail Rotor Head and Drive Shafts.
Previously, KONGSBERG has participated in the F-16 program with production and maintenance of Adapter Penguin MK3 missile, Air Circulation Equipment (Cooling Turbine), Brake & Anti-Skid System. KONGSBERG has also been involved in the maintenance of the following artillery: L70 Anti-Aircraft Gun and 20 mm Anti-Aircraft Gun.
-
NH90
Foto: Forsvaret -
Sea King
Foto: Forsvaret -
AW101
Foto: Forsvaret
SEA KING
- MRO for gearboxes and rotor heads
- Main rotor head
- Main gear box
- Intermediate & tail gear box
- Drive shafts
- Ongoing for over 30 years in the Norwegian market
NH90
- KDA exclusive license for MRO of MGB for International market
- Total 52 helicopters
AW101
- MRO and testing of MGB, IGB and TGB for International market
- Total 44 helicopters
Kongsberg has for more than 30 years performed overhaul and repairs on the sea king sar and lynx aircraft dynamic components.
Related news
Repair and overhaul of dynamic components for helicopters in civil and military service
Step by step
-
1. Pre-inspection stadium
- The component is dismantled down to all the assembled pieces
- Cleaned for dirt and oil to allow for inspection
- Removal of paint where NDT is required
- Trained inspectors with long experience will go through all ingoing parts to discover any abnormality
2 Inspection
- All components are cleaned
- Visual inspection
- Dimensional inspection
- Special inspection due to experience or incidents
- NDT (non-destructive test): Magnetic particle and fluorescent penetrant inspection. Eddy current and X-ray inspection
- Release of work
3 Rework and modifications of components
- Repairs of components according to approved procedures
- Installation of oversize liners
- Introduction of modifications after written procedures
- Restoration of surface protection as Cadmium plating, chromic acid treatment for magnesium, chromate conversion coating
- Stopping and removal of corrosion
- Painting
4 Assembly process
- Local repair of surface treatment
- Use of special tools during assembly
5 Assembly and test
- All hoses and tubes are pressure tested
- All valves are tested in accordance with their manuals
- Components are tested for correct torque, flow and oil leakage
- Main components such as the main gearbox are tested in a special testbench simulating operating conditions