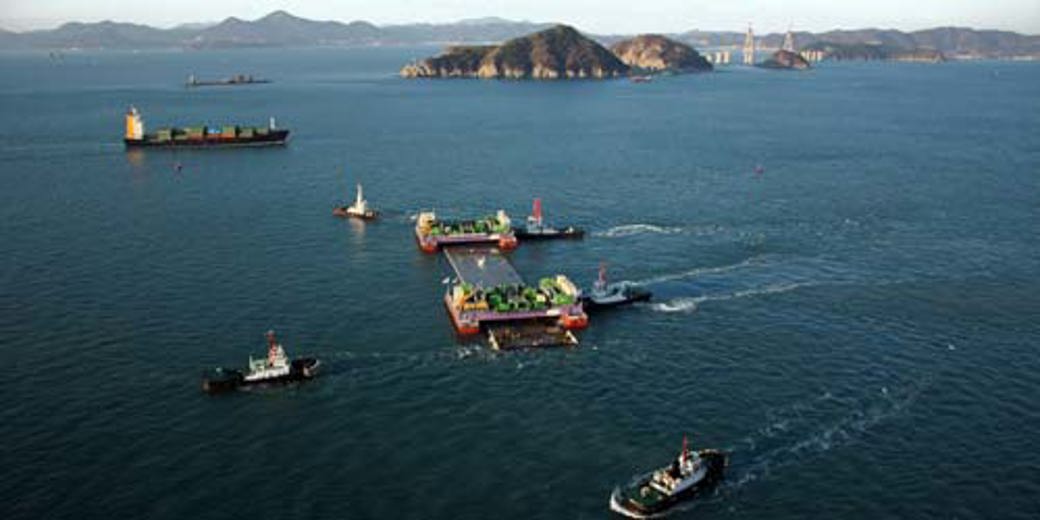
Client-orientated teamwork 50m below sea level
Positioning specialists Geocon and Kongsberg Maritime collaborate on product optimisation in immersion operations.
Immersing tunnels in open sea involves minimal positioning tolerances and often extreme conditions. Positioning specialist Geocon, a subsidiary of Dutch top-five construction company Strukton, collaborated with Kongsberg Maritime to optimise the use of acoustic measuring equipment in immersion operations – an example of client-centricity from both parties.
Adventure
Engineer Bart-Jan Ruesink, who holds primary responsibility for measurement operations at Geocon in Utrecht, the Netherlands, walks through the warehouse where his equipment stands waiting for shipping. He says: "This is the Kongsberg Portable HiPAP® SSBL/USBL system, the acoustic measurement system we used as a backup in South Korea. That's where our joint adventure – our partnership with Kongsberg – began."
That adventure was part of the Busan-Geoje Fixed-Link Project in South Korea; a bridge-and-tunnel connection stretching across a total of 8.2 kilometres in order to aid traffic flow between two economically prominent areas. The contract for the immersion of the 3.2-kilometre tunnel at a depth of 50 metres below sea level was awarded to Strukton Immersion Projects, which specialises in the engineering and immersion of tunnels, and Ruesink's team from Geocon, a company specialising in measurement and monitoring in offshore situations.
Inventing your own methods
The exceptional conditions under which the tunnel elements needed to be immersed in South Korea confronted the engineers from the Netherlands with a wealth of new questions. Ruesink explains: "The big thing about this project is that it's in open sea – up to 1.5 kilometres offshore! Normally, like in the case of a canal, the measurements can be taken from land using prisms fixed to the measurement tower, access shaft and a number of total stations onshore prior to immersion. Provided the shaft remains above water, we can measure.
"Or so we thought. In South Korea, this method didn't work. First of all, when you're measuring across the water so far from shore, reliability can diminish to an alarming extent. Secondly, the access shafts are not suited to such depths. Consequently, we found ourselves faced with an interesting challenge. In other words, if the old method didn't work, we would need a new one. But we needed to invent that new method ourselves. In doing so, we listened carefully to, and paid close attention to, the interests of the client. For instance, where the risks lay and what the client's worries were. Taking those worries off the client's hands – or, in other words, hedging the risk – was our top priority. In this respect, we're a kind of insurance policy."
Tight deadlines
Ruesink and his team were involved in all the milestones of the immersion process in South Korea: The design of all the measuring equipment, and its installation onto the elements under construction in the dock; steering of the course to, and positioning at, the immersion locations using GNSS data; and, finally, measurement and monitoring during the actual immersion process. Ruesink says: "We realised all too well that the success of the operation depended on the accuracy of our information, because an immersion team leader without accurate information is like a manager without eyes and ears. This gave our activities extra focus."
Not least because the immersion operations had to be carried out to extremely tight deadlines. (The area is notorious for typhoons in the summer, so the team were unable to work in this period.) Given the limited timeframe, delays caused by a misaligned or, worse, damaged element were out of the question, especially given their colossal length and weight of 180 metres and almost 50,000 tonnes respectively.
Contact
"From the moment the element is hoisted above the point of immersion, we use the taut wire we invented and developed specifically for this project. The taut wire is a measurement technology that, aided by a taut cable, measures the distance and angle to the immersed element. We concurrently used the Kongsberg Portable HiPAP® SSBL/USBL system. This technology worked well, but not as accurately as we had hoped, achieving an accuracy of 0.20 metres compared to the taut wire's 0.03 metres. At that point, we started an intensive process with KONGSBERG, with the aim of achieving more accurate results. In this process, they went above and beyond the call of duty as a supplier, even after successfully immersing the final tunnel element. We were pleased to see KONGSBERG strive for the same accuracy we were aiming for, and with the same drive."
Wideband
The solution was based on the Kongsberg cPAP® and cNODE® acoustic wideband system, which has since been successfully tested in an immersion operation for the North-South metro line in Amsterdam in 2012. According to Ruesink: "This project involved the immersion of three tunnel elements in the original IJ estuary behind Amsterdam's Central Station. These tunnel elements were 141 metres in length, 11.3 metres wide and 7.6 metres high, with the contract permitting a tolerance of only 3.5 centimetres. Two of the tunnel elements needed to be immersed in narrow, water-filled circular cofferdams, which could potentially negatively affect the acoustic measurements as a result of reflections. We also came up against geometric limitations, such as the limited width of the tunnel element and the required deck layout between which the KONGSBERG equipment had to be installed. Through thorough preparation, which included many simulations in APOS, we succeeded in finding the optimum positions."
Forging ahead together
The three tunnel elements were immersed using the traditional approach with total stations. The KONGSBERG system ran in the background aided by cPAP® and cNODE transponders using the Cymbal acoustic wideband protocol. Ruesink continues: "Based on the measurements obtained with the two technologies, we were able to raise a glass that evening to our partnership. The acoustic system had amply met the specified cm-accuracy accuracy requirements, which meant we were able to add another proven method to the range of measurement technologies we offer our clients. This represented another step forward in immersion technology."
With this focus on the interests of the client, Ruesink fulfilled his company's philosophy of providing the best possible solution for every project, assessing and meeting the client's needs, and, in the event of ‘impossibilities', persevering until a solution is found: "In terms of proactiveness and commitment to our interests, we found the right partner in KONGSBERG."
Suiting the action to the word
Geocon and KONGSBERG consequently agreed to partner up again on future projects. When exactly that will happen will depend on the project and its specific requirements. Either way, Geocon will be partnering again with sister company Strukton Immersion Projects on an offshore project near Venice. Secured by Strukton Immersion Projects, the project involves performing the measurement activities during the transportation and immersion of eight concrete caissons, each weighing 21,000 tonnes. Ruesink expands: "A movable barrier will be erected on the caissons to protect Venice against floods. The preparations are already well underway, and the project is scheduled to be carried out in the summer of 2014."
Software
Prior to the project in Venice, Ruesink says the next step will be taken in the development of the wideband. "What we recently did in Amsterdam was to test the accuracy of the technology. What we are now doing is to incorporate the information the Kongsberg wideband solution with cPAP®, cNODE® and Cymbal provides us into our software system. In the system, all of the data we receive from the measuring points – such as the position of the elements, but also the forces on the hoists, and the water in the ballast tanks – is interconnected."
Not a puzzle
According to Ruesink, however, it is not the intention that this should result in some kind of puzzle on which the immersion team leader must base their decision: "The actual immersion process is a tense, three-day operation that requires the utmost concentration non-stop from start to finish. For this reason, we filter out all redundant information, so that the people carrying out the operation are only shown the essential parameters in a clear and simple layout they can rely on."
This also shows that measurement during immersion operations goes far beyond the ‘dry' collection of as much data as possible. Ruesink: "You need to know what you're doing and speak the client's language – whether they're based in Seoul, Amsterdam, Venice or Ireland."
Mentality
Given its experience with in-depth, long and complex projects, Geocon is an attractive player for large future projects. Ruesink concludes: "The bigger the project, the greater the importance of proper measurement and monitoring. Also, it's not only about the technical aspect, but also the human aspect. It means working under pressure, but, above all, communicating effectively with each other. You need to maintain contact, both in the preparatory and execution stages. This is exactly what we are experiencing in our current joint adventure with Kongsberg Maritime. From the perspective of your own discipline, you try to create added value for the client on the project – up to 50 metres below sea level. And we could undoubtedly go deeper. With proper, open collaboration, anything is possible!"
Profile
Netherlands-based company Geocon specialises in positioning systems for inshore and nearshore projects. It operates between the disciplines of geodesy and hydrography, and provides added value with its mastery of the full (and complex) chain of engineering, execution and aftercare in complex positioning projects. Geocon is, like sister company Strukton Immersion Projects, a business unit of Strukton. In its home country of the Netherlands, Strukton is a renowned top-five construction enterprise in the areas of infrastructure and accommodation. Strukton's primary focus is ensuring mobility, confluence and continuous operation.