State-of-the-art Integrated Automation System and DP System supports unique HiLoad concept.
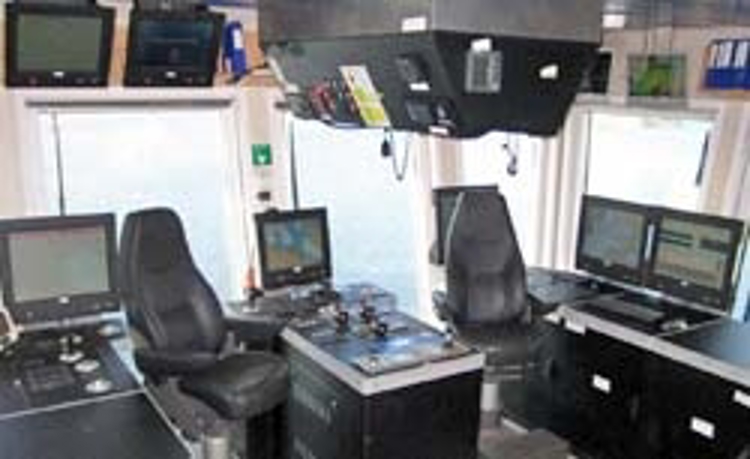
The 27th January 2011 was a milestone in the development of the unique Remora HiLoad DP as it completed its final sea trials before live field implementation. HiLoad is a revolutionary deepwater offshore loading terminal, made possible by innovative vessel design and the use of a cutting-edge Kongsberg Maritime Integrated Automation System (IAS).
Built at the Aibel Shipyard, Haugesund, Norway, HiLoad is the first vessel in a new generation of generic offshore loading systems that through state-of-the-art technology, including Remora's patented HiLoad Attachment System and Kongsberg Maritime's IAS; which includes K-Pos Dynamic Positioning, K-Chief marine automation, K-Bridge, and fire, safety, and emergency shutdown system; can control the position of a standard oil tanker that does not have its own thrusters or DP system. This mobile system can be deployed at any field and used for the safe and efficient transfer of oil from an FPSO to any size and type of tanker, effectively replacing the need for a shuttle tanker.
The K-Chief automation system aboard HiLoad monitors and controls the Ballast, Power Management, Thruster Control, Machinery and bilge system. There are approx 2500 I/O (signals) with Field stations placed around the ship connected to each other and the operator stations on the bridge via redundant network. The IAS includes custom automatic ballast sequences for docking and undocking of a tanker, which are based on predefined sequences of valve and ballast pump operation, with back pressure automatically controlled via integrated PID controllers.
The K-Pos Dynamic Positioning system controls the position of HiLoad when alone and when connected to an oil tanker loading oil behind a FPSO. Because the application is brand new, Remora and Kongsberg Maritime had to develop several unique processes for the DP system.
"Early in the project several big challenges that needed special attention were identified," comments Pål Borge Korneliussen, Group Manager, Application / DP & Manoeuvring Offshore, Kongsberg Maritime. "The size of the tankers can vary from Aframax to VLCC and because of this range we needed to develop a method for calculating the hydro dynamic model for the different oil tankers. We also had to consider the massive change in displacement when HiLoad connects to a tanker.
"The most challenging operation for the HiLoad is connecting or disconnecting the oil tanker. For the final sea trial using the Aframax tanker SKS Tana we implemented local reference systems between the HiLoad and the Oil tanker; Kongsberg Maritime's own RADius and a Fanbeam system. This gave HiLoad the possibility to determine the heading and the position of the oil tanker relative to itself. A modified Follow Target function made the approach towards the oil tankers safe.
"The size and shape of HiLoad is unique so there was a significant effort to establish the correct parameters. All in all the final 21 day sea trial was successful for the customer and for the Kongsberg Maritime systems aboard HiLoad," continues Korneliussen.
"There were a number of obstacles and challenges during the project period, but through good communications, resource management and highly skilled engineers Kongsberg Maritime has made a successful delivery to support a cutting-edge concept that can provide tangible improvements for offshore operations," adds Project Manager Glenn Edvardsen.
The DNV approved HiLoad DP is the first of a planned series of HiLoad vessels. (Approximately) 13 oil companies representing the majority of the world's oil production observed the sea trials and have shown interest in using the system.