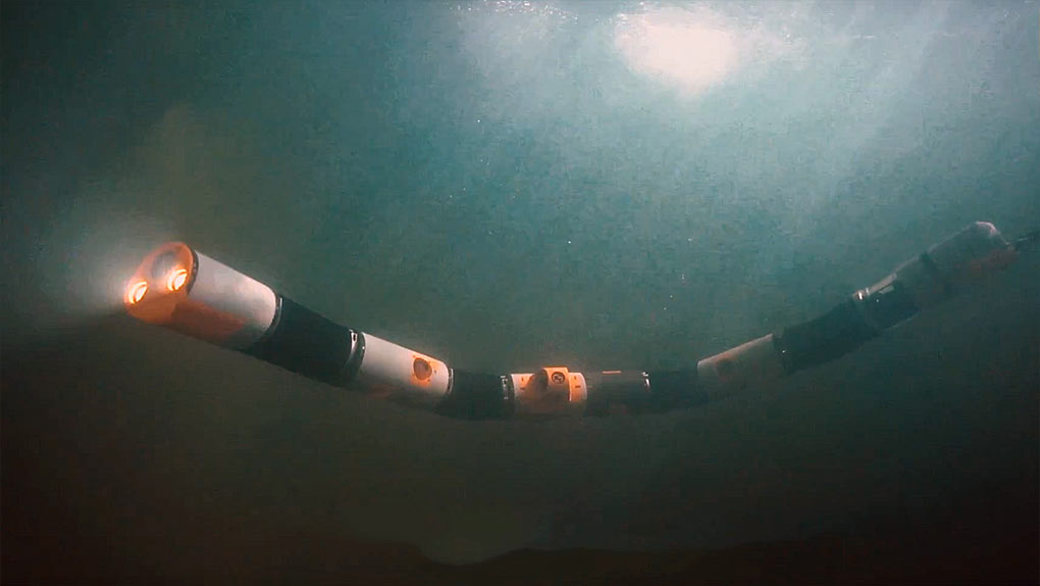
Eelume: A Flexible and Subsea Resident IMR vehicle
Eelume signifies a leap in subsea robotics capabilities. It is a modular, flexible robot capable of swimming like a snake, or being propelled by conventional thrusters. Eelume is designed to reside subsea to provide immediate response to unpredicted inspection, maintenance and repair (IMR) requirements.
Introduction
The oil and gas industry has a growing demand for new and innovative solutions for inspection, maintenance and repair (IMR) of subsea installations:
- The number of subsea installations for oil and gas production are increasing.
- Existing subsea infrastructure is ageing.
- More complex structures are deployed subsea.
- The industry poses strict demands for inspection and maintenance.
- Information retrieval and preventive maintenance can reduce costly repairs.
IMR operations within the subsea oil and gas industry are today carried out using ROVs (remotely operated vehicles) deployed from large surface vessels. The main cost driver of these operations is the surface vessel, which has very high day rates. Oil & gas operators experience significant costs every year related to rental of surface vessels to provide a continuous IMR capability on existing subsea installations. To reduce IMR costs, oil and gas companies therefore have a significant need for reducing the use of surface vessels.
Subsea residence is the key to reduce the need for surface vessel-based ROV operations and thereby reduce current IMR costs. A resident IMR solution can be permanently installed on subsea installations and carry out IMR routinely and on-demand.
This paper presents the Eelume vehicle concept and the development of the first Eelume prototype. In addition to being subsea resident, its articulated structure allows the vehicle to combine the functionality of several types of more conventional subsea vehicles and thereby cover a broad range of operational scenarios.
The company Eelume AS is based in Trondheim, Norway and has entered a partnership with NTNU, Statoil and Kongsberg Maritime to produce resident IMR robots for oil and gas operators.
Vehicle concept
Eelume takes its name from an eel, and the ability to illuminate the dark recesses of the ocean.
The Eelume concept is illustrated in Fig. 1 and emerged from more than 10 years of research on snake robotics at NTNU and SINTEF in Trondheim, Norway. The concept involves a new type of flexible subsea vehicle comprising a chain of joints, thruster modules, and various payload modules. A unique feature of the vehicle is its ability to change shape. It has dexterity and hyper-redundancy not previously available in commercial inspection and intervention vehicles for oil and gas operations.
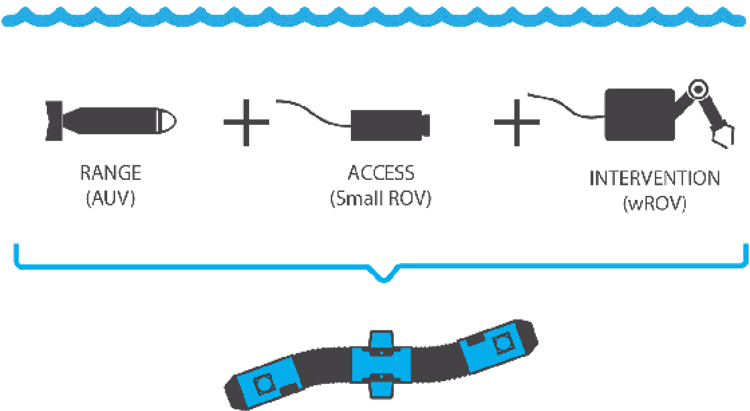
The shape-changing capability allows the vehicle itself to act as a robotic arm. The flexible body and narrow cross-section provide significant advantages over existing ROVs, including the ability to perform IMR in constrained locations of subsea installations where existing ROVs are too large to gain access. During inspection and intervention tasks, the vehicle can hover by means of ducted lateral and vertical thrusters installed along the flexible body.
The narrow body of the vehicle also allows for transit over long distances like a cruising AUV (assuming the vehicle is tetherless and battery-powered). The vehicle therefore combines IMR capabilities of existing ROVs and the cruising and survey capabilities of existing AUVs. The flexibility of the vehicle and its ability to cover a large range of operational scenarios make it an ideal candidate for a subsea resident IMR solution. The main advantages of the vehicle concept are summarized in Fig. 2.
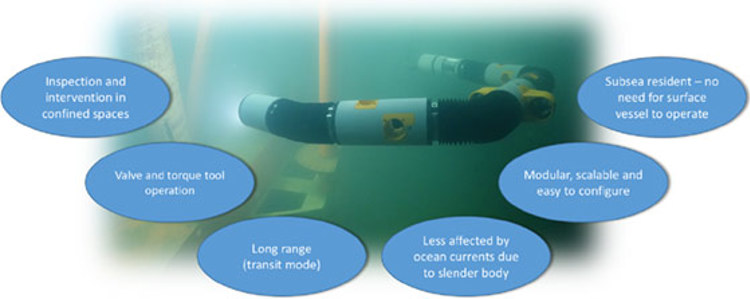
Vehicle prototype
The first Eelume vehicle prototypes are shown in Fig. 3 and were developed and demonstrated in 2016. The purpose of the development was to verify and demonstrate the basic functionality of the vehicle in a realistic maritime environment.
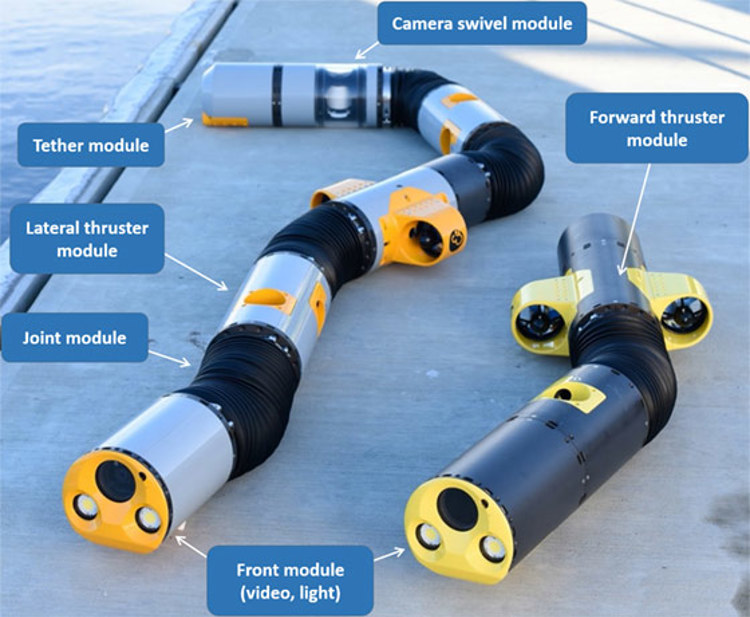
The prototype has a depth rating of 150 meters and its main function is to provide live HD video to a topside operator. The vehicle is powered from the topside operator station through a tethered connection. This tether also contains a fiber for communication.
A modular concept was chosen to increase the flexibility of the vehicle and to simplify the configuration of the vehicle for different operational requirements. Six types of modules were developed with an identical mechanical and electrical interface to make the modules interchangeable. Fig. 3 shows the six types of modules, as well as two different vehicles realized by two different combinations of these modules. Table I provides a description of each module, while Table II summarizes the main characteristics of the large vehicle shown in Fig. 3.
Table I. The modules of the prototype
During 2016, extensive testing of the prototype has been carried out, including several sea trials down to 150 m depth. The testing has been successful, and the main required functionality and underlying design concepts of the vehicle were verified. The following images were captured during these tests.
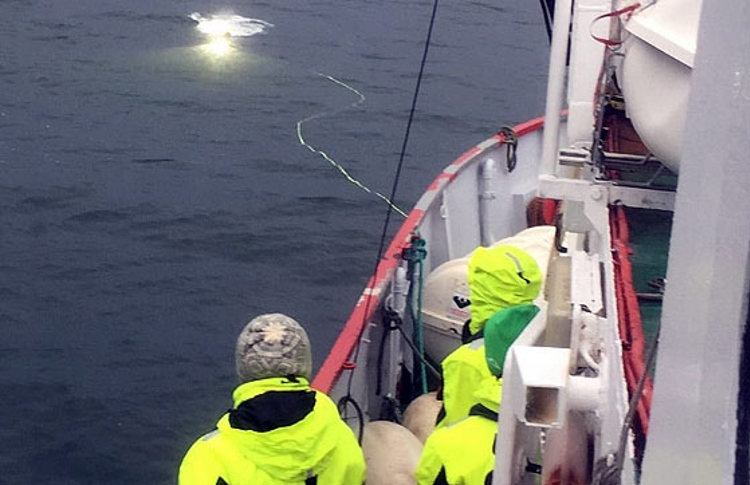
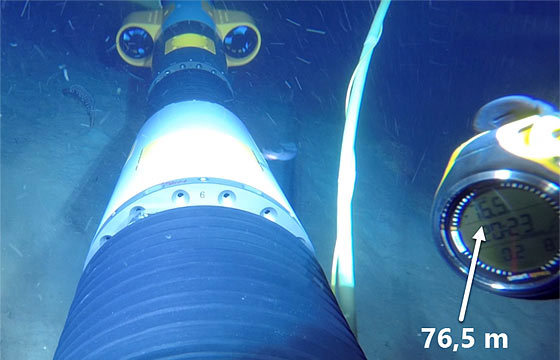
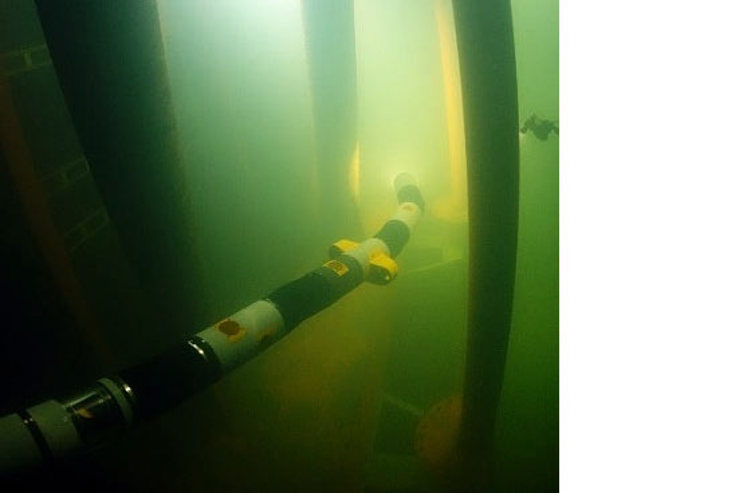
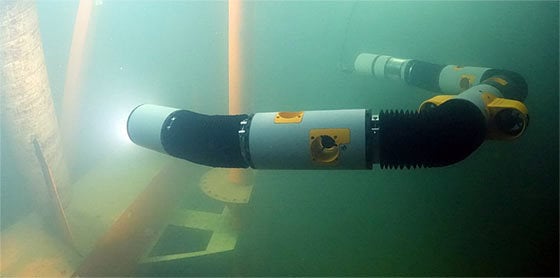
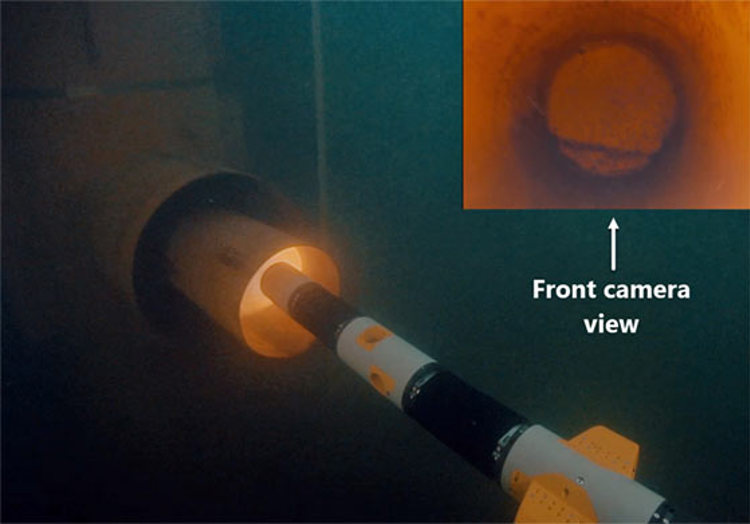
Future developments
Subsequent versions of Eelume will introduce new capabilities. The second generation vehicle, which will be demonstrated in 2017, will have a depth rating of 500 meters and be configured for light intervention. It will be capable of operating a torque tool, cleaning tool, and other tasks as required. Operation of torque tools can be carried out by exploiting the dual arm nature of the vehicle and shown in Fig. 9. In particular, one end of the arm can grab hold to fixate the vehicle, while the other end can operate the tool.
The third generation Eelume, planned for 2018, will be capable of tether-free operations. It will be equipped with internal batteries and on-board processors enabling the vehicle to transit between structures autonomously. When close to a template, Eelume will connect wirelessly with high-bandwidth bidirectional communication when close to a structure. At that stage an operator can take over control.
Eelume will be resident on the seafloor close to a template or subsea factory (see Fig. 10). Operators sometimes require access to IMR capabilities at short notice, particularly in the case of emergency shut downs. With Eelume vehicles located adjacent to subsea templates and equipment, the delay normally introduced in waiting for an ROV to arrive on scene is eliminated.
The dock will be configured to provide power and communication to the vehicle through a wireless interface. The long term plan is to have Eelume remain in situ for up to 6 months at a time. This will require a flexible design including storage for swappable tools.
Network communication and power could be provided by connecting to the operator's subsea network. Alternatively, there is potential to utilize a surface buoy acting as both a communication gateway and power supply, ideally generating energy through renewable methods.
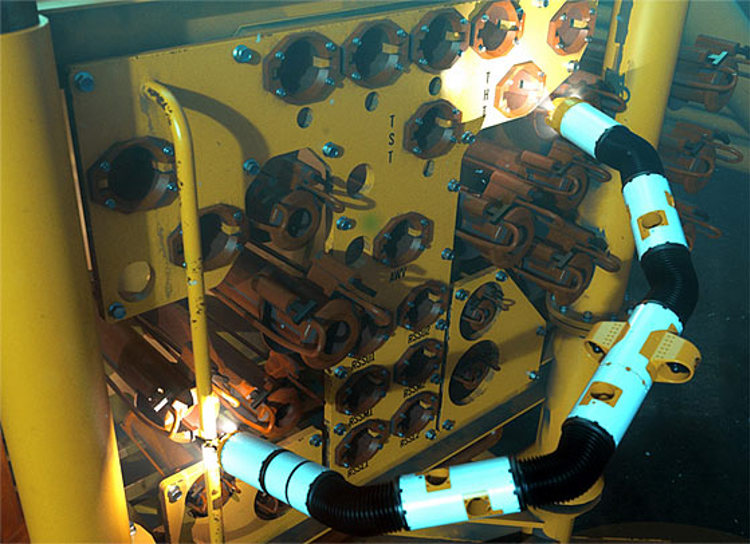
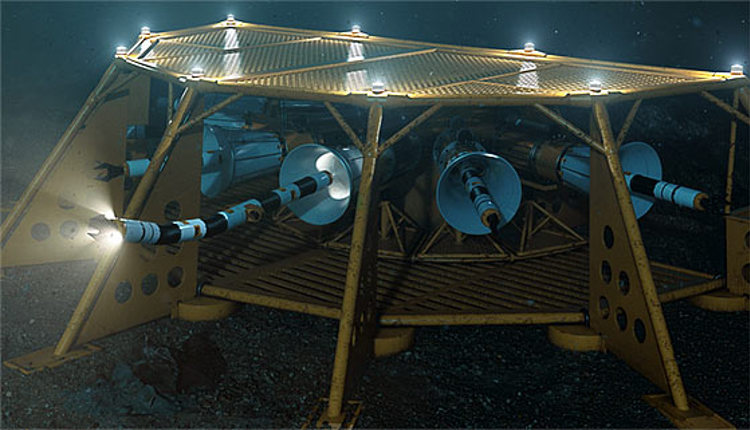
Conclusion
Eelume offers a capability that no other underwater vehicle can. It can be resident, autonomous or controlled by an operator. It can also change its shape to reflect the requirements of the task at hand. As a resident seafloor robot Eelume can conduct routine inspection and maintenance tasks. It can also be available for emergency intervention. Eelume will augment existing methods and technologies, offering a reduction in OpEx and total cost of ownership to operators.
Authors
Pål Liljebäck, CTOEelume AS, Trondheim, Norway
Richard Mills, Director of Sales Marine RoboticsKongsberg Maritime AS, Horten, Norway