Hydroid, Inc., a subsidiary of Kongsberg Maritime and a leading manufacturer of marine robotic systems, announces its integration of the Seaglider® Autonomous Underwater Vehicle (AUV) Division into its organization.
The transfer of Seaglider® from Kongsberg Underwater Technology, Inc. (KUTI) allows Hydroid to leverage complementary technologies and markets across the REMUS and Seaglider® product lines. Integrating Seaglider® into Hydroid also increases the range of technical solutions and program management support that can be offered to customers.
“We look forward to leveraging the strengths of these advanced technologies to enhance both product lines and offer a more diverse set of solutions to our customers,” said Duane Fotheringham, President of Hydroid.
KUTI’s current office in Lynnwood, WA has been remodeled so that Hydroid will occupy approximately 18,000 square feet of space for Seaglider® engineering and manufacturing. The integration of the Seaglider® team grows Hydroid to over 200 employees.
KUTI will no longer be a subsidiary of Hydroid and will align its business with Kongsberg Maritime, Inc. in Houston, TX. It will continue to provide Full Picture solutions to customers, focusing on sonars, acoustics, subsea docks and monitoring, and underwater science sensors.
About Hydroid, Inc.
Located in the U.S. and a subsidiary of Kongsberg Maritime, Hydroid is the world’s most trusted manufacturer of advanced Autonomous Underwater Vehicles (AUVs). Our marine robotics systems provide innovative and reliable full-picture solutions for the marine research, defense, hydrographic and offshore/energy markets.
MEDIA CONTACT
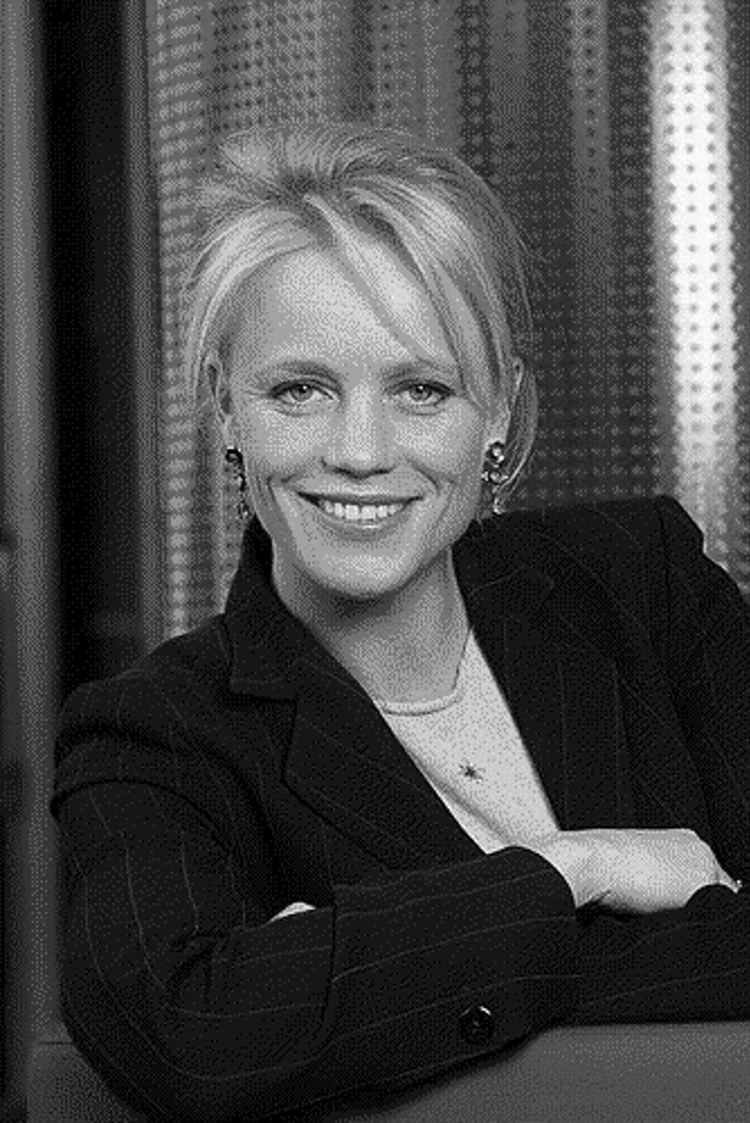