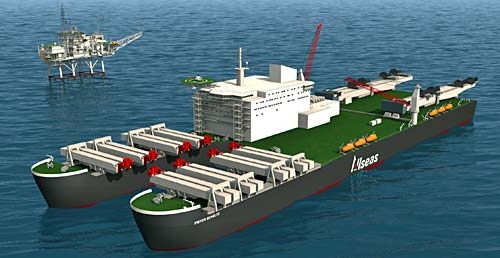
Integrated dynamic positioning & manoeuvring solution
After the successful launch of Audacia in November 2007, Allseas is now fully committed to its next construction vessel - Pieter Schelte - which will take the pipe laying specialist into new territory by providing heavy lift and platform removal capability. With the Dutch company Imtech Marine & Offshore as contractor for the power and drive solution, Kongsberg Maritime will supply a unique integrated Dynamic Positioning and manoeuvring solution, tailored to the operations of Pieter Schelte.
Outstrip the existing global fleet
Pieter Schelte will be one of the most advanced construction vessels in operation, and is due to enter service in 2011. With the U-shaped slot at the bow, the vessel can position itself around a platform jacket prior to the removal process. For field abandonment/lifting operations, the vessel will have a capacity to handle topsides of 48,000 metric tons and jackets up to 25,000 metric tons. In pipe laying mode, with a tension capacity of 1,500 (upgradeable to 2,000) metric tons, the vessel will by far outstrip the existing global fleet.
The right solution
"The operational capabilities of Pieter Schelte are enormous and thus require state of the art quality control systems. Considering the complex operations that we will be involved in, we put a lot of trust in the integrated Dynamic Positioning and manoeuvring solution," says Gerard Stenfert, E&I lead engineer, at Allseas. "With the past good experience we have with Kongsberg Maritime, we are confident that they will provide us with the right solution."
Complete solution
The Kongsberg Maritime integrated Dynamic Positioning and manoeuvring concept relies on a distributed and open system design, which employs a fully backed-up system-wide standardized communication network. The communication network integrates the K-POS Dynamic Positioning, K-Thrust thruster control, and K-Chief machinery automation systems, into a complete solution with unique positioning and manoeuvring capabilities required for e.g. the planned heavy lift operations.
Two fully redundant bridges
The vessel employs two fully equipped redundant bridges; forward and aft (in separate fire zones). The Kongsberg Maritime supplied equipment communicates either via the redundant LAN network or via the alternative also redundant serial network. The two bridges thus provide full redundancy for each other and the total system is redundant to an extent that surpasses the DP class 3 requirements.
"Built-in blackout prevention features such as dynamic load limitation of propulsion and thrusters drives, monitoring of load sharing devices and load shedding are all features needed to provide a robust Dynamic Positioning and manoeuvring solution to Pieter Schelte," comments Birger Evensen, sales manager, Kongsberg Maritime. "Although every project is different, the sheer scale of Pieter Schelte represented numerous challenges as we developed this complex solution. We had to employ the total sum of our knowledge and experience to create a system capable of positioning and manoeuvring such a massive vessel, and are confident that we have achieved this aim."