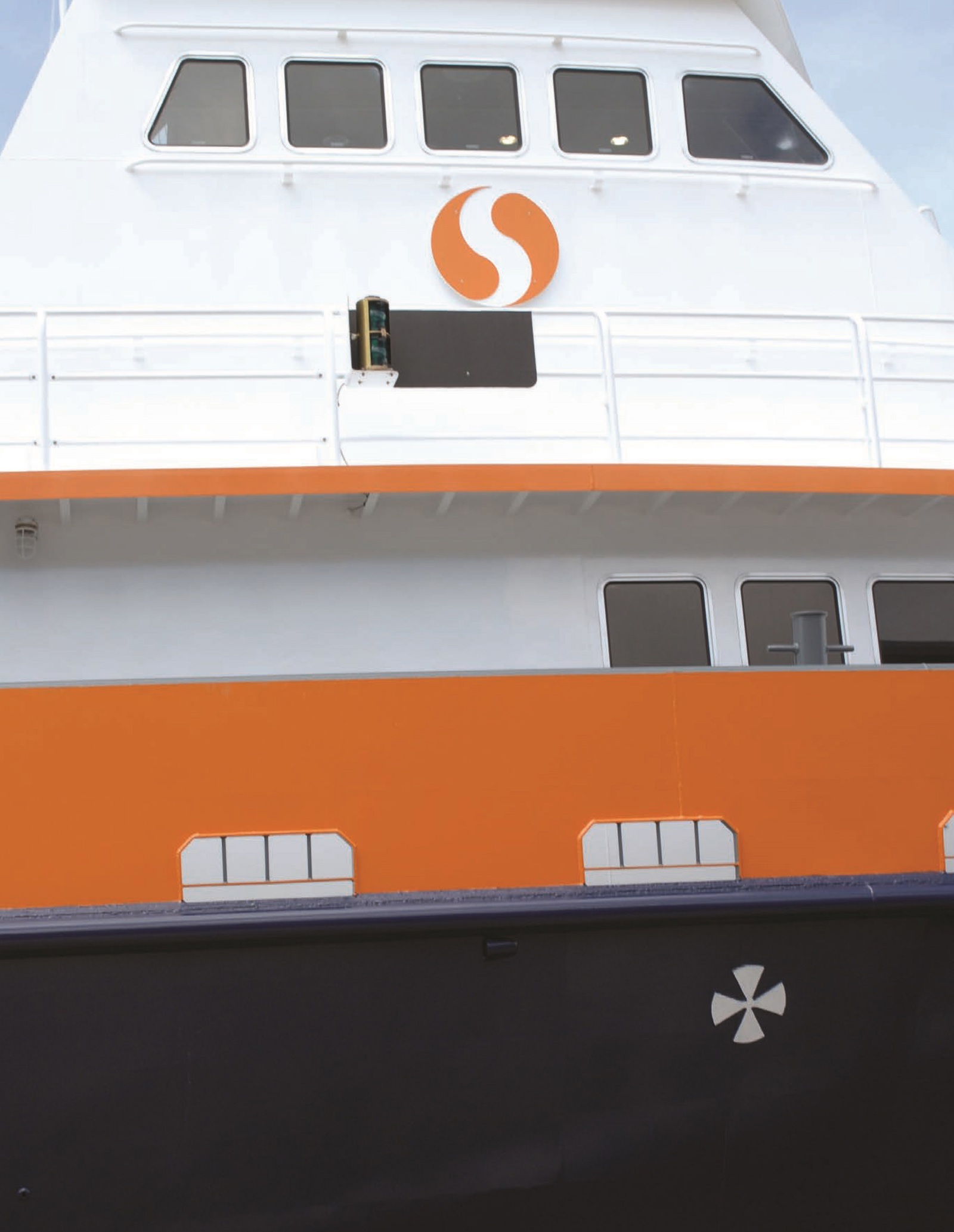
Transporting people from A to B. SEACOR’s customers have a simple requirement that can be met using proven vessel designs and technology. This hasn’t stopped SEACOR Marine in ploughing millions into improving its vessels’ comfort, safety and efficiency though.
-
Text:Kongsberg Maritime Communication
-
Gunvor Hatling MidtbøVice President, Communications
Aiming to exceed customer requirements has paid off for the Houma, Louisiana based crew boat specialist, as it is one of the largest crew boat operators in the world and is considered by many as the most innovative and forward looking.
“SEACOR is always looking at ways to push the envelope – to go bigger and faster with more advanced technology. We are always looking to add innovations to the vessel platform, which enhances the benefits to our customers. It’s very fun to be part of that,” explains Joe McCall, SEACOR’s project manager for aluminium crew boats and all-round crew boat design and operation guru.
Joe’s reputation as an expert in the field has come through decades of working with offshore vessels and through following in the footsteps of his dad, Norman McCall. Norman, who celebrated his 88th birthday in March this year, started McCall Boat Rentals Inc. (later known as McCall/Cameron Crew boats) in 1967 and in 1969 he built his first crew boat, the Phyllis McCall.
Norman is responsible for several industry firsts including the first four engine crew boat in 1970, the first five engine crew boat in 1984 and the first 6 engine crew boat in 1989. In 1996 McCall/Cameron Crew boats merged with SEACOR Marine and the innovation kept coming; by 2002 Norman and SEACOR had built the largest ever crew boat for its time, the 190ft Granville C McCall.
PIONEERING SPIRIT
The pioneering spirit of his father has certainly rubbed off on Joe, whose work over the past 16 years at SEACOR and before that with McCall/Cameron Crew boats, has resulted in a number of his very own firsts. Notably he was behind the first ever DP1 crew boat, the first ever DP2 crew boat and now, with the forthcoming 190ft CrewZer Class vessels SEACOR Lynx and SEACOR Leopard, the world’s first DP3 crew boats.
“SEACOR is always looking for innovation to apply to crew boats to make them a safer platform for cargo and personnel transfer offshore,” explains Joe. “DP improves our station keeping ability. We implemented our first DP system on the Phillip Alan McCall in 1999. There were challenges with integrating the equipment and with training our personnel to operate it. That was the first step, however, and that led us to where we are today.”
Ted Murphy, Senior Sales Manager at Kongsberg Maritime Inc., has been working with SEACOR for over thirty years and has played an important role in developing DP technology for crew boats alongside Joe.
“The guys involved at SEACOR were Tony Jones, Joe’s dad Norman and Joe, and from Kongsberg Maritime it was me, Lars Moen and Sam Weather- “I feel that they all,” explains Ted. “No one had ever even dreamed about the possibility of putting DP on a crew boat but Tony called one day so Sam and I went down and met with Joe and his dad.”
Joe explains that because crew boat dynamics are so different from other offshore vessels, there were a lot of challenges with the DP software at first: “The Philip Alan McCall was never designed as a DP vessel, so many modifications to the thrusters, engine and gear controls, and other systems were necessary. We were working on controllable speed propellers at the time too, which would prove very beneficial later, but there were a lot of challenges to overcome.”
Ted takes up the story: “So what we had to do was let it work for three months and take in all the data and write the software based on this. Once we had established how the software and crew boat worked together then it became easier from that point forward. A key breakthrough was when SEACOR recognised the need to hold the bow in position correctly. You might ask, ‘what’s the point,’ on a crew boat the bow is usually out of the water. Joe and Norman came up with the idea of putting in a drop down thruster. That was the one key factor that made all of this go forward.”
THE MAGIC NUMBER
Since those pioneering days of developing the concept of DP for crew boats, SEACOR has been one step ahead of the competition. The latest generation CrewZer class vessels have been designed around the redundancy and segregation that a full DP3 system requires.
SEACOR Lynx and SEACOR Leopard are under construction at Gulfcraft Shipyard in Franklin, Louisiana and due for delivery in the first half of 2013. The vessels will be the first crew boats to operate using an ABS Class DP3 system, affording them the highest degree of manoeuvring safety available today. The CrewZer Class features a twin-hull design that enables speeds of 46-knots, which is more than twice that of conventional crew boats. “They really are cutting edge, state of the art vessels,” enthuses Joe. “They are designed to optimise passenger comfort. This includes first-class seating, passenger amenities and the equipment on board to minimise pitch and roll while underway. We want passengers to be as comfortable as possible. They should be well rested when they arrive at their final destination.”
The key difference between DP2 and DP3 is increased redundancy, especially for fire and flooding. For DP3 multiple engine rooms and segregation of cable are key aspects. The DP computer is on the bridge and thrusters are at the other end. If there is a fire in the middle of the vessel it could affect thrusters at either end. DP3 allows for this so that the vessel can continue to manoeuvre safely during and after the loss of a thrusters or system because of the multiple layers of redundant systems.
“The main reason for going DP3 is that it’s a standard, a regulatory benchmark. It affords a level of safety above DP2 that can be measured and recognised by customers. It’s not a job requirement but an additional layer of safety,” says Joe.
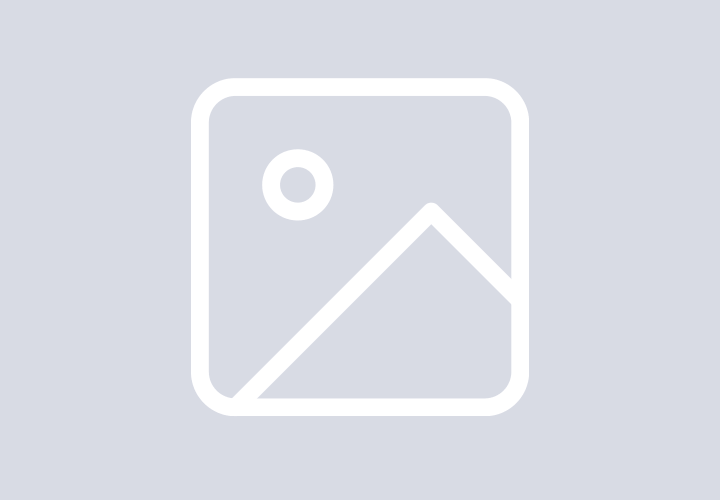
Dynamic moves: SEACOR is using a collaborative approach to set new sector standards.
VITAL INGREDIENT
It’s safe to say that DP crew boats are SEACOR’s domain, and Joe’s speciality. He readily admits though that he is not a DP specialist so he depends on his vendors to support his vision for his latest project. According to Ted Murphy, moving from DP2 to DP3 is very much a team effort, with the onus on SEACOR and CrewZer vessel designers Incat Crowther to create a vessel that allows for the redundancies and segregation the class demands. Working closely together has proven to be a vital ingredient for success.
“Collaboration is very important, because nobody knows the equipment as good as the supplier,” adds Joe. “I’m not an expert on DP, I’m not an expert on engines, I’m not an expert on transmissions but each of my vendors are so I rely on them to work with me so that I understand the capabilities, benefits and value the equipment brings to me.
“I’ve been working with Ted and Kongsberg Maritime for many years. I feel that they know me and if I can express my needs to them they can help us make a package of all the various components and put that together to make a successful vessel.”
Kongsberg Maritime has been SEACOR’s sole supplier for DP for crew boats. According to Joe they recognised a long time ago that Kongsberg Maritime has a quality product so collaboration with them makes perfect sense in that it has supported SEACOR in enhancing its capabilities towards customers. At the end of the day, keeping customers happy with a reliable and safe method of transportation is why SEACOR is at the top of its game.
“Our crew boats operate in some of the most remote places in the world and Kongsberg Maritime has always been there with technical support to keep our equipment running. We want a relationship with our partners to span decades, for the life of the vessel and partners that are ready and keen to work on future projects. I think Kongsberg Maritime fits that bill.”