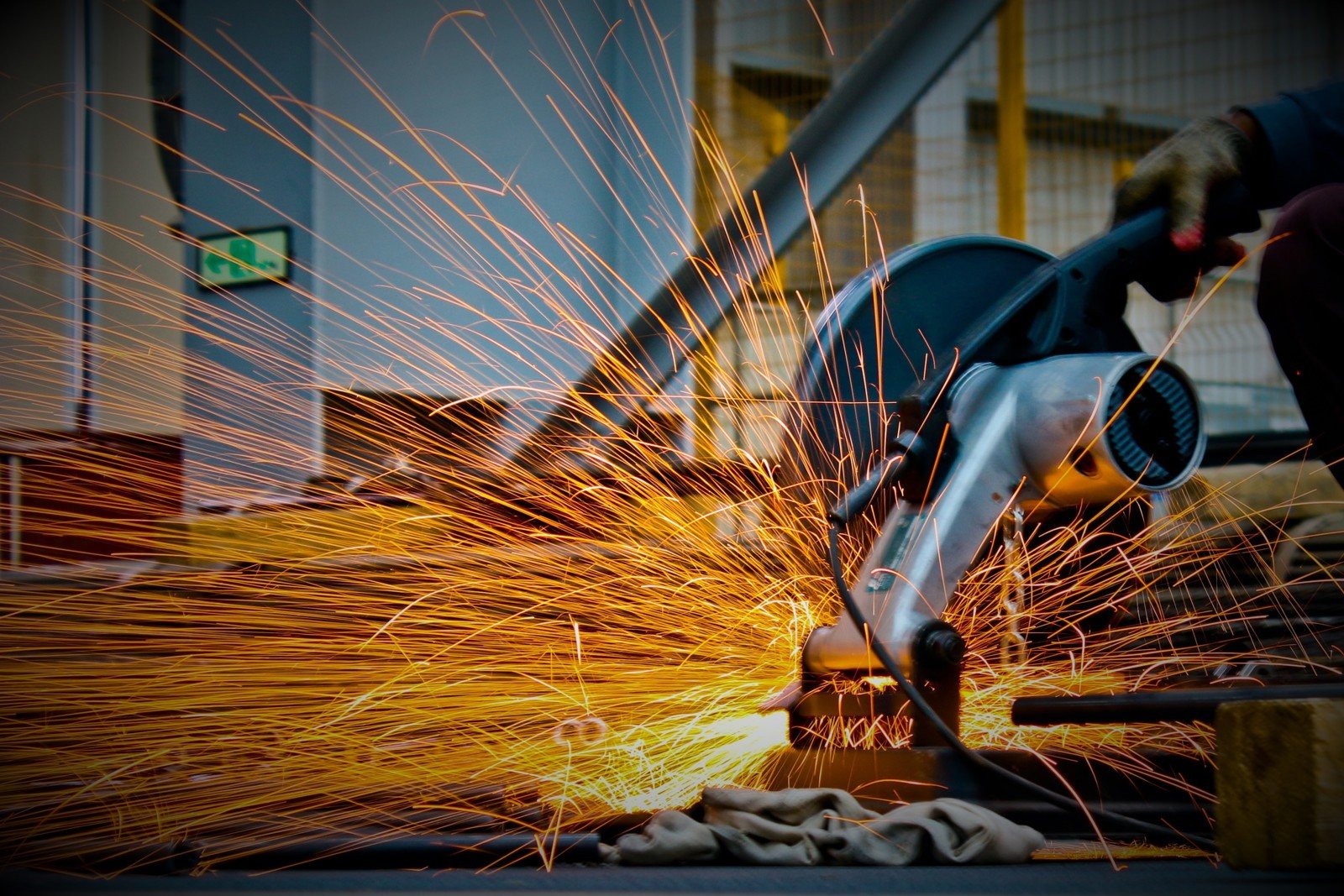
A tough team for testing times
Not even a global pandemic could stop COSL, KONGSBERG and NOV’s project team from achieving its energy efficiency goals.
-
Text:Marketing & Communication Department
Photo:©COSL
-
Gunvor Hatling MidtbøVice President, Communications
There’s nothing quite like a challenge to form a strong team!
And when the challenges just keep piling up, the team that has to face them becomes something really special.
So Torfinn Kalstø, ICT and OT manager at COSL Drilling Europe SA, discovered when he asked Kongsberg Maritime to help him bring his vision for energy-efficient rigs to life.
Getting started
“It started back in 2014, when we began to map out our power consumption,” he says. “We looked at all our applications, from drilling to platform management to accommodations. We were thinking about hybrid applications, or the possibility of heat exchange from the mud we churn up when we’re drilling. Anything that would help us use energy more efficiently.”
The research stage turned up a few surprises. Never having attempted anything of the kind before, Torfinn and the team at COSL expected to see some industry-wide assumptions being confirmed.
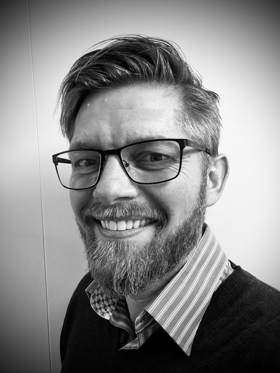
“We’ve shown that it’s not rocket science to achieve huge savings — you just need to have a broad view, to see the synergy between the different systems that operate together on a rig. We’d never have achieved that without the effort everyone put in. The extra hours, the humour, the sense of fun — it’s all been a really exciting adventure.”Torfinn Kalstø, ICT and OT Manager, COSL Drilling Europe SA
“Before we did this mapping everybody in the industry believed that the biggest energy consumer aboard the rig would be the drilling and/or thruster applications,” he says. “But what we showed is that most of the actual power consumption comes from keeping the coffee warm, putting dinner on the table, heating the hotel and so on.
“It’s something nobody believed, and it’s still hard for people to understand. They are sure that if they have such huge machinery on board the rig, it will be the largest consumer of power. But I would say more than 50 per cent, maybe as much as 60 per cent of the energy on the rig is going towards the accommodation and utilities not related to drilling and positioning.”
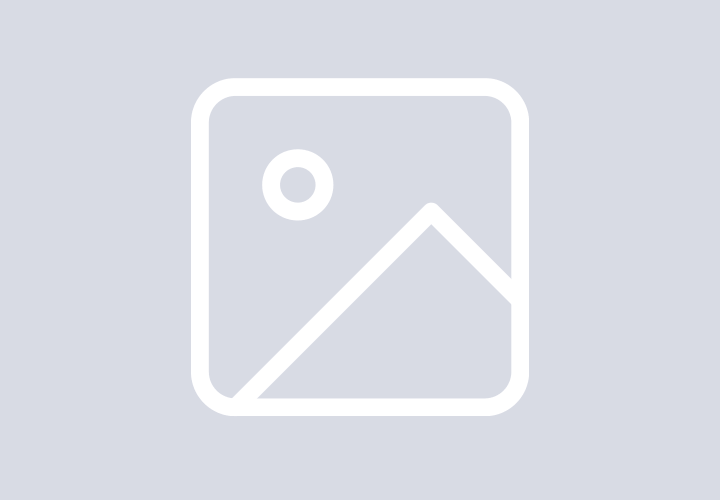
“We’re a relatively small organisation,” says Torfinn. “We don’t have a lot of resource in terms of engineers or specialists. We already had a great relationship with KONGSBERG, so we asked them to help us out.”
Coincidentally, KONGSBERG was already looking into the same issue – how to monitor, reduce and improve energy flow on offshore rigs without adding ‘negative capital’ in terms of additional equipment.
“One of the huge benefits of that concept was that it could potentially allow quite drastic changes to operations, saving energy and fuel, without adding a lot of equipment on board,” says Morten Firing, Kongsberg Maritime’s Operations Manager in GCS and Aftermarket Projects. “That would mean savings in terms of operational cost and in terms of equipment and environmental costs.
“So we were looking at these ideas, but they were still very much on the drawing board, we hadn’t brought them to life. Then, a year ago, COSL came to us and the project really got started.”
It’s in the nature of pioneering projects that they need to move fast. So the timeline for turning the concept into reality was tight — and got tighter still after the initial meeting of the project team. The challenge was enormous: drilling operations on board a rig are a complex combination of safety and operationally-critical energy consumers.
On top of that there are applications that control the rig’s stability, operations that maintain living accommodation, and national and international legislations and certifications that must be complied with.
The project team, as well as including COSL and KONGSBERG, involved participants from drilling specialists NOV and representation from Global Maritime, a marine, offshore and engineering consultancy, which helped with FMEA studies. The key to success would be communications between the various teams and their IT and communications systems, while maintaining compliance with international maritime rules.
Everything was moving ahead according to schedule, which Morten describes as “challenging but manageable”. The plan was to get everyone involved on board a rig that had been docked, which would provide a stable version of the real operational environment to run calculations and tests on.
Then came challenge number two.
“The way this was supposed to happen was that we would be on board the rig lying ashore, in a very calm situation, and have the time we needed to get things done,” says Torfinn. “However, just as we were about to start, COVID-19 took hold.”
Morten adds: “That was a huge challenge. We were pressed for time, offices were closing down, no-one knew what was happening. We decided we needed to shut down the office and ship everything onto COSL Innovator to prevent the entire project closing down.”
After consultation with independent assurance and risk management experts DNV, that’s exactly what happened. Two projects — to increase energy efficiency on board and to update or retrofit existing KM systems — were moved offshore.
The circumstances and ongoing uncertainty created by COVID-19 meant the COSL Innovator energy efficiency project couldn’t be completed in full, although it was taken as far as possible. The retrofit, however, was implemented as planned, and included:
- ICS Retrofit for K-Chief 700, K-Thrust 720, K-Safe/ESD
- Rebuild of the fuel piping system to the diesel generators to fit 14 coriolis fuel flow meters.
- Gyro to MGC upgrades.
- DGPS and HiPAP upgrades.
After completing everything they could on COSL Innovator, the team shifted focus to the COSL Promoter, positioned in the Troll field in the North Sea. This time the team would be able to carry out the full energy efficiency project. And to keep up with the demanding schedule, their delicate task would have to be completed offshore. That wasn’t their only challenge. The unavoidable restrictions placed on the first project meant they had no opportunity to test the energy efficiency innovations fully.
“Our project team was really tested with these deliveries. The sheer size of the two briefs, and the relatively short time available, meant we had to be determined, think innovatively to overcome technical challenges and collaborate with customers and third-party suppliers for a successful delivery. These projects have shown we are the reliable partner customers are looking for.”Morten Firing, Operations Manager, Kongsberg Maritime, GCS AMS – Offshore & LNG
“It was quite extraordinary,” says Torfinn. “We actually executed the entire first complete project out in the field on board COSL Promoter while it was in full operation! We just jumped right into it. The whole project team shipped out, we were all so eager to keep going. It was an adventure.”
An adventure that called on everyone to use every resource at their disposal — and on KONGSBERG to pull it all together. “It’s quite common that we take the lead on projects like these,” says Morten. “We are a large organisation, we have significant resources, so we’re well-placed to manage everything, including third-party suppliers.
“That was a huge benefit for this project, because we were able to communicate directly with NOV and Global Maritime as well as with COSL to find the most efficient solutions that worked for everyone.”
As if grappling with real-life conditions on board an active drilling rig wasn’t enough to deal with, the team still had to find clear channels of communication for what they were doing — internally and externally.
Kongsberg Maritime Senior Software Engineer Alexander Lithun faced the task of integrating communications between drilling specialist NOV’s systems and Kongsberg Maritime systems. “I was assigned software responsibility from day one,” he says. “My job was to understand what we were supposed to deliver.
“The standard power management system is a typical delivery from us. The main obstacle was to understand how to integrate our systems with NOV’s, and how to exchange the functionality between them. In fact, it involved creating entirely new systems, because this idea had never been delivered to any operational rigs. It was new to both NOV and us.
“We knew there would be no additional equipment for the energy efficiency project brought on board COSL Promoter, so we would have to achieve our goals purely through the magic of software.”
While Alexander was wrestling with the software solutions, Torfinn was attempting to gain buy-in from clients and investors.
“There were lots of obstacles involved in convincing other parties that our approach was the way forward,” he says. “Part of that was trying to make it easy to understand. When you’ve been working on something for a long time it’s easy to get into details and names and numbers that don’t mean anything to anyone else. We’d be going on about something that seemed perfectly obvious to us, and the clients just wouldn’t be getting it.”
Another key factor, Torfinn continues, is that oil industry clients don’t traditionally focus on energy efficiency. “Clients’ operational teams usually have nothing to do with their environmental teams, so fuel and emissions is not something they are concerned about on the operations side,” he explains.
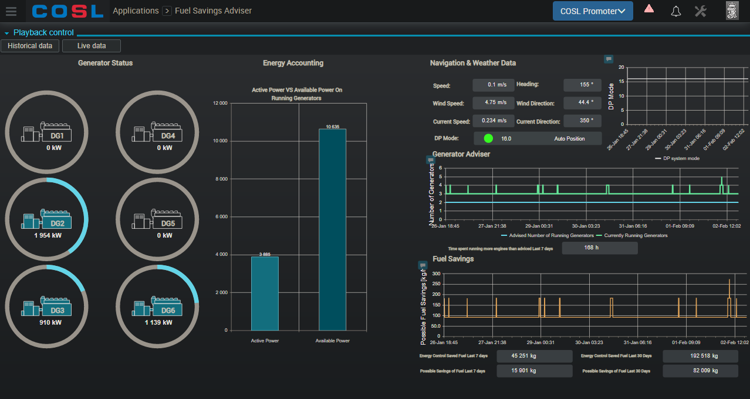
“They have a different division handling environmental concerns, so they don’t care if you use this much energy or emit that much CO2 because it doesn’t involve their budget. That can make it really hard to convince clients, especially when they’re so big that it’s difficult for them to see the whole picture.
“Right now, for example, we’re working with Chrysaor. They’re a smaller team, and they see the whole thing — operational, environmental, logistics, accommodations — they see everything. So when we tell them we can cut their costs by so many million dollars per operation, they listen.”
Challenging acceptance
“They’d seen something about our work on the news, and wanted to know what we were up to,” he grins. “And they were really thrilled with the idea. In fact, everybody who has some understanding of what we’re doing is pretty thrilled.
“We have developed a different way of thinking. We’ve challenged the known, because before now everybody just accepted how much energy you need on board a rig or a vessel. They accept how much fuel you burn – everything has just been accepted all these years.
“Now that we’ve started to challenge this acceptance, we are discovering a lot of potential, not only in what we’re doing now but in the fact that there is so much more that we haven’t looked into yet. We’ve shown that it’s not rocket science to achieve huge savings — you just need to have a broad view, to see the synergy between the different systems that operate together on a rig.”
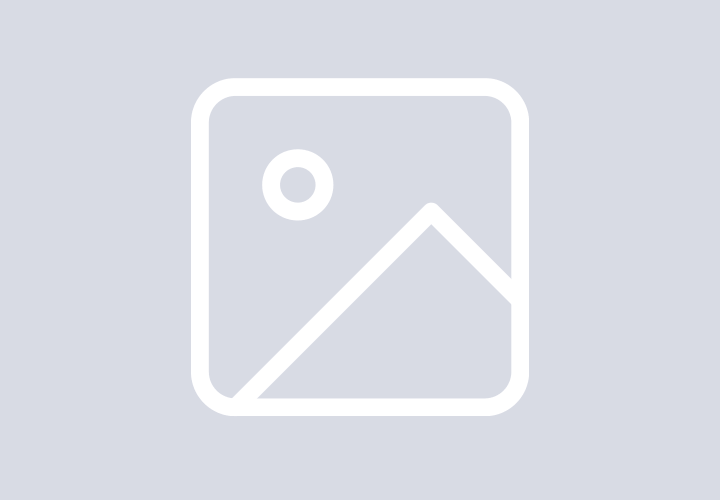
#squadgoals
“I’ve been in this business for 20 years,” said Morten. “I’ve been part of many projects like this one, but I’ve never experienced team bonding and team spirit like we had on this project.”
Torfinn agrees, saying: “I’ve been so impressed with everyone. We’d never have achieved what we did without the effort everyone put in. The extra hours, the humour, the sense of fun — it’s all been a really exciting adventure.
“Yes, there were hard, long days. There were so many other challenges to be overcome. People missing off the helicopter that somehow were compensated for. Situations on board the rig that we didn’t have full control over. A lot of small things, as well as major issues. But we all understood what we were part of.
“Something just kicked in and all of us together made it work. Despite all the challenges, it could never have happened if we’d done it in any other way. Everything would have stopped on 13 March 2020 and we’d be sitting here today with nothing to talk about!”
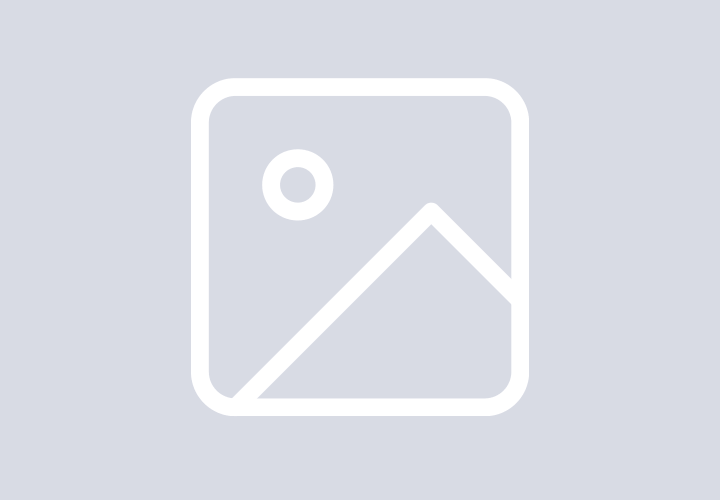
Several people during final project meeting involved from COSL Chryasor Customer DNV GL Class Company and Global Maritime 3 party verification.
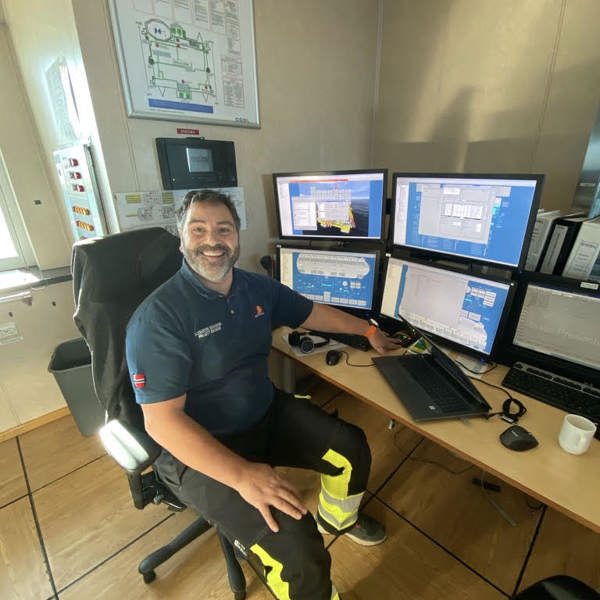
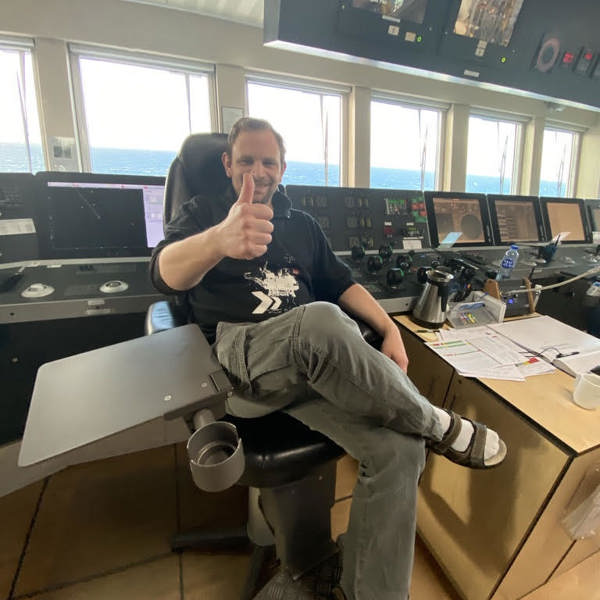
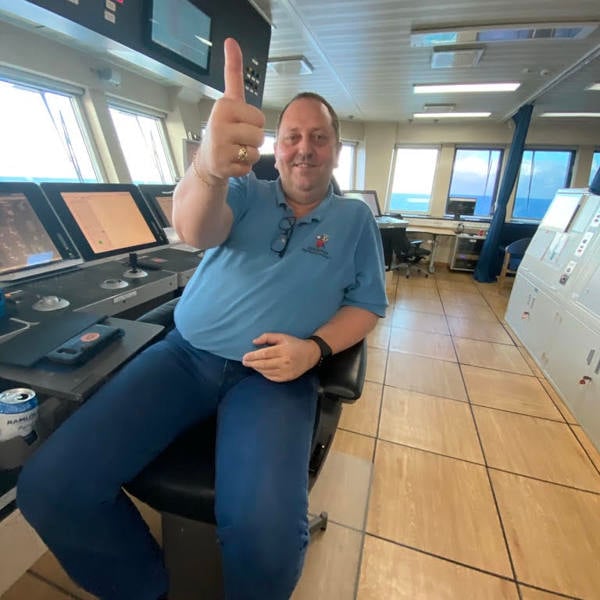
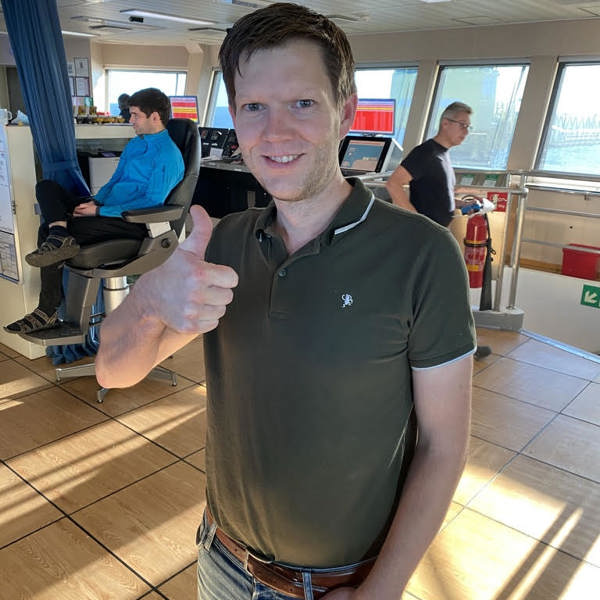
In this case, it’ll be extending the current project to the remaining rigs in the COSL fleet. “The project is live on two of our rigs — COSL Promoter and COSL Innovator,” says Torfinn. “I trust that within the next few months we’ll begin the next rig, bringing our whole fleet on board.
“That’s the first step. The next will be to start challenging what we know now. So we might look at reducing energy use in the accommodation area as the place to cut energy. A lot of that energy goes into heat, for example. Right now we pump heat onto the sea surface or up into the clouds. But maybe we could be using it to brew coffee.
“The end goal is to help make the entire industry more sustainable. To help us become climate neutral. We know we’ll never have zero emissions, that’s just not possible. But if we can use all our energy as efficiently as possible, we can reduce them and at the same time offset our impact on the environment.
“As a bonus, we’ll also increasingly reduce costs and improve efficiency in our operation. It’s a win-win.”
In 2020, after several years of concept research and development around improving energy efficiency in drilling operations, the team at COSL Drilling Europe AS decided to take their concept live.
Together with Kongsberg Maritime and drilling specialist NOV, they launched a major project to reduce energy consumption on COSL rigs in the North Sea.
‘Energy Control’ aimed to reduce greenhouse gas emissions, maintenance costs and fuel use for rig engines and generators. It started from an extensive mapping programme that created an extraordinarily detailed outline of energy use across the entire rig.
“We made it possible to see everything that consumes energy on a rig,” said COSL’s project leader and ICT and OT Manager Torfinn Kalstø. “We monitored most of the consumers, the impact of the weather and waves, and we discovered a lot that we didn’t know before.”
The initial project to reduce emissions and improve efficiency was to take place on COSL Promoter, a sixth generation harsh environment semi-submersible DP3 rig already laying claim to record low emissions for its type.
The rig’s six Wärtsila Vasa 12V32 diesel generators, developing 4,800kW each, had always run continuously during drilling operations. Analysis had shown, however, that full capacity was rarely used.
At the same time, NOV examined historical data for parameters such as rig movement, hook load and the number of generators, and delivered a software update to optimise energy utilisation for large consumers.
Based on COSL’s findings and NOV data, KONGSBERG developed advanced, targeted solutions to control energy production and distribution on board. The result? Three of the six engines could be shut down.
The remaining generators work at higher loads, which is highly beneficial to the diesel engines, with more efficient fuel consumption and reduced carbon build-up. That in turn has a positive effect in terms of improving the working environment, reducing noise and cutting back unnecessary maintenance.
The whole creates dramatic savings both in costs and emissions. Annual fuel consumption is cut by approximately 2,300 tonnes, CO2 emissions by 7,300 tonnes and NOx by 125 tonnes. That’s an overall saving in both fuel and emissions of more than 25 per cent, almost three times what COSL had anticipated at the beginning of the project.
A patented dynamic positioning system developed by KONGSBERG means the inactive generators will still come on board should additional power be required. It anticipates thruster requirements and adapts the energy flow accordingly, preventing reactive spikes in demand. At the same time, its information management system (K-IMS) collects performance data and uploads it to the cloud, so performance can be monitored, reviewed and verified against benchmark data.
“Before now, we only knew on average what was going on,” says Torfinn. “Now that we know in detail, now that K-IMS can provide us with accurate replication of most of the digital values on board, we can compare performance and plan for improvements.
“We have so much data now that we are creating an operational centre in the COSL main office, where it will be available at all times. That way we can evaluate each discipline and operations as a whole. We can see the relations between drilling, marine, safety, engines, pumps, and so on. Which means we can also see — and share — the actual value or actual reduction in our planned next steps.
“Our focus has changed from simply reducing consumption for economic reasons. We are now actively aiming to reduce our environmental footprint — and we are increasingly finding that also means reduced costs and increased efficiency. So we’re achieving even more than we’d hoped from this project, and we look forward to continuing to develop and advance those achievements across the industry.”