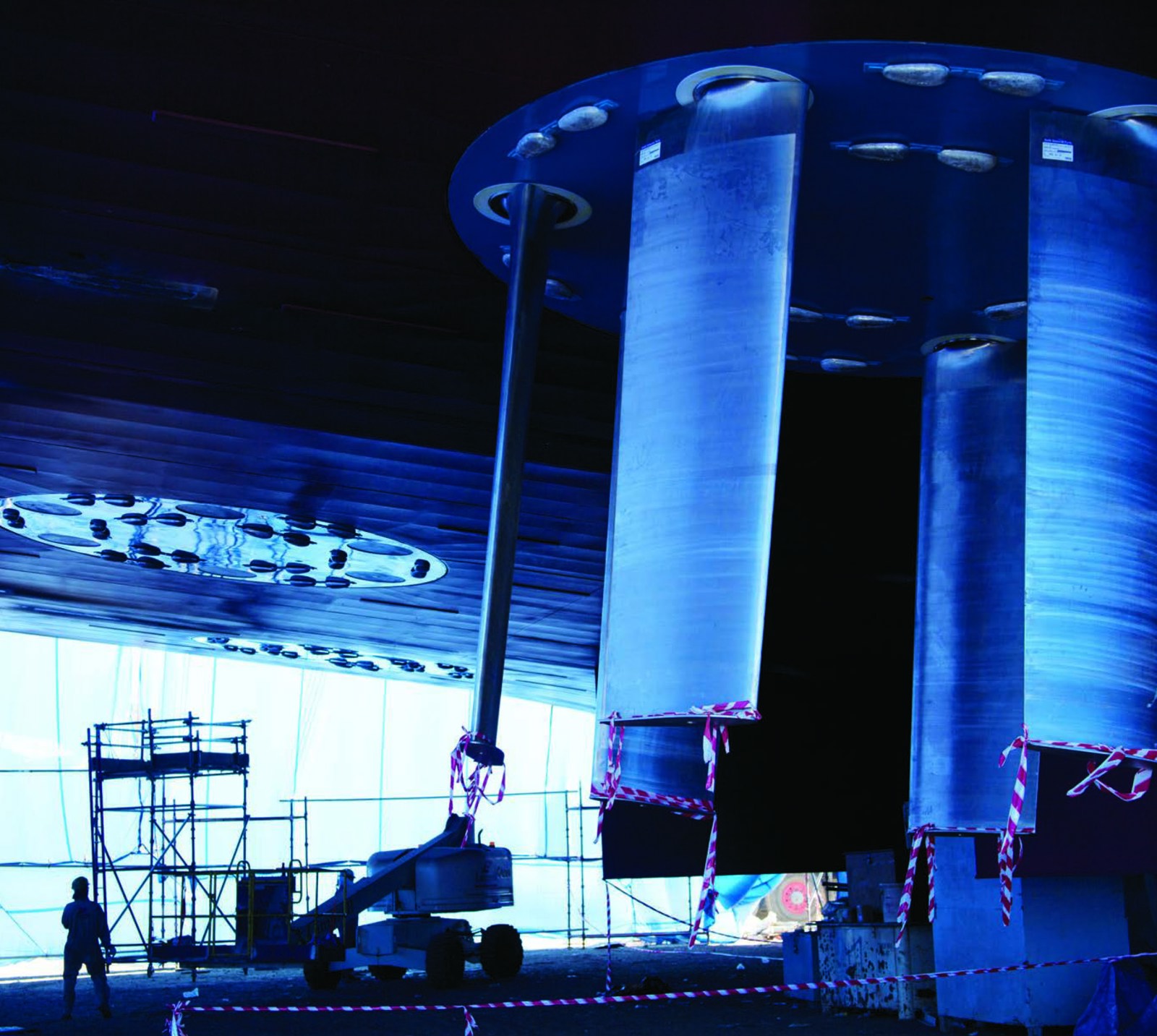
Winds of change for Fred. Olsen
After more than 35 years of building and operating oil and gas vessels, drilling units, FPSOs, and tankers, Fred. Olsen Windcarrier saw an opening in the wind turbine installation market. It promptly ordered two large newbuilds, designed specifically for this purpose. The Full Picture visited the Lamprell shipyard at Jebel Ali, UAE, to see the first vessel, Brave Tern, nearing completion.
-
Text:Kongsberg Maritime Communication
-
Gunvor Hatling MidtbøVice President, Communications
With an increasing focus on wind as a viable longterm energy option, several wind turbine installation vessels (WTIVs) are currently being built around the world. The offshore wind-farm industry is in its early days and there is still much discussion over the optimal WTIV design – size being one of the most contentious issues.
After weighing up its options, Fred. Olsen Windcarrier decided to construct vessels at the larger end of the scale. According to Site Manager, Sturla Fjoran, it was all about striking a balance between operational and market considerations.
“There are many factors to consider during the design phase, but our vessels are designed to handle both installation of the bottom mounted foundations as well as the topsides including tower, nacelle and blades. Basically, we are constructing vessels that we believe will be suited to deliver more than 90 percent of the contracts in the market.
“Some deep-water foundations will be in excess of our capabilities, but we haven’t yet seen any turbine designs that our new vessels cannot handle. In our judgement, it would have been excessive to build bigger vessels, as the market is not ready to pay the corresponding price; on the other hand, the smaller vessels cannot transport enough turbines at a time, are limited to shallower waters and are too slow,” he points out.
Regardless of size, installing offshore wind farms requires the WTIVs to maximise both deck space and variable load, enabling them to transport and install several turbines at once without needing to reload. This is one of the major design features of the Fred. Olsen Windcarriers. To free up as much deck space as possible, the vessels are outfitted with an 800-tonne capacity crane, which wraps around one of the legs. This makes room for an exaggerated 3,200 square metres of deck space – which can support up to 5300 tonnes.
SERIOUS JACKING CAPABILITY
These dimensions – along with the need for a frequent and rapid jacking capability to minimise installation times – put an extreme demand on the jacking system. To address this, the vessel is equipped with a heavy-duty, continuous hydraulic jacking system.
Whereas a regular jack-up vessel will often only jack up once a month, the WTIVs are made to jack up and down 300 times a year. The trade-off is that the cylinder legs are not capable of going to a water depth greater than 50 metres, but most wind farms are being installed in waters shallower than that limit.
This made the cylindrical leg, allowing for a fast and extremely robust jacking system, an obvious solution compared to a truss leg with a fatigue sensitive rack and pinion jacking system.
In order to reach the required tolerance levels, its cylinder legs had to be accurate within millimetres over their eighty-metre length. Lamprell’s Senior Project Manager Darren MacDonald says completing the design and building the prototype jacking system was a significant feat.
“The tolerance in this system is like nothing I’ve ever seen. Constructing the legs required extreme fabrication and dimensional control. Installing the hydraulic components was also a complicated process because the whole system had to be installed sequentially,” he says.
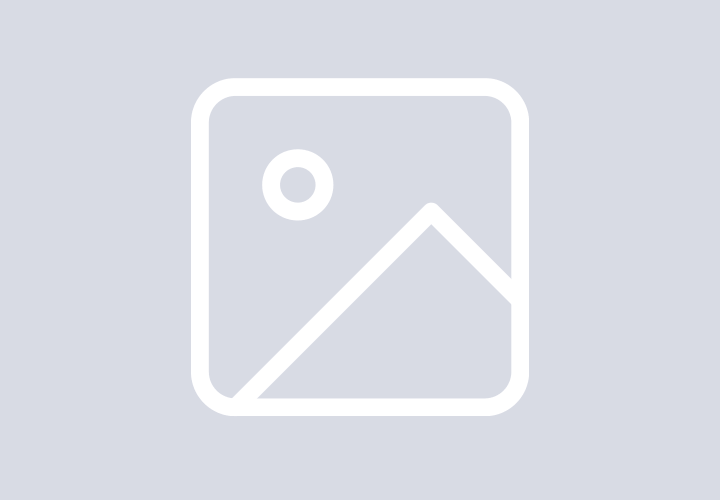
Fleet building: expect to see a demand-driven explosion in the number of WTIVs.
VERSATILE VESSELS
As insurance against a possible downturn in the offshore wind market, the Fred. Olsen Windcarrier vessels can be converted to oil and gas vessels. Fjoran explains how this was a consideration during the design phase.
“We wanted to have a fall-back option. This led to certain design features such as the ship-shaped hull and the size, which makes it better suited for oil and gas purposes. We also worked closely with Det Norske Veritas (DNV) to ensure that the vessel complied with relevant rules so that it could easily be prepared without major conversions for various operations like accommodation, construction and well-maintenance,” he says.
Fjoran hopes, however, that this flexibility will not be required.
“We believe that the offshore wind market has a strong future. At the moment, European offshore wind is not meeting the ambitious growth projections with some scheduled projects slipping considerably. Consent, financing, and the grid and infrastructure required for offshore wind farms have been causing delays. However, we believe that in the long term, wind will form an important part of many nations’ total energy requirements,” he says.
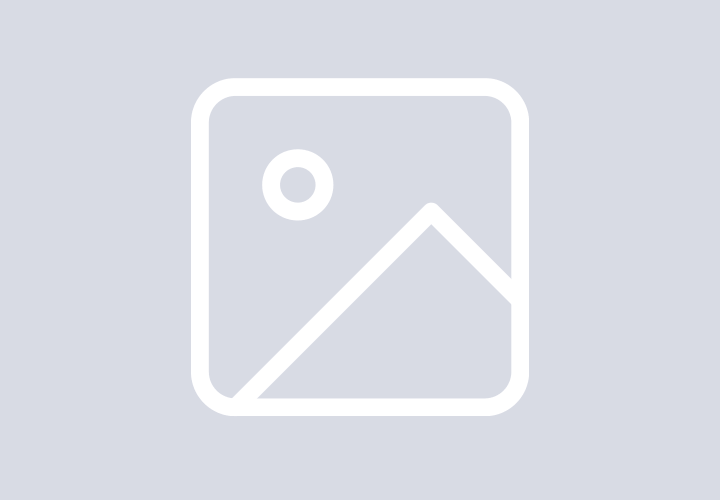
“We are constructing vessels that we believe will be suited to delivering more than 90 percent of the contracts in the market”. - Sturla Fjoran Site Manager, Fred. Olsen
AGGRESSIVE SCHEDULE
It is an impressive operation. At any one time, there are more than 2500 employees working on the WTIVs – Brave Tern and Bold Tern (and so far there has been no time lost due to accidents or injury).
Because of the aggressive nature of the schedule, McDonald says his project team had to think of creative ways to streamline the construction.
“We cut the first steel just sixteen months ago. It was a concurrent design and build approach, meaning that much of the design was still being done after construction had started, so we could meet the deadline. At this stage, we are on target to launch in mid-February as planned,” says MacDonald.
He concludes that he and his team have learned much throughout the challenging project.
“Admittedly, the nature of these vessels, their sheer size and the fact that they are under a new class notation has resulted in a very challenging design and construction process. But I have a fantastic team working through these issues on a daily basis and it has been a great opportunity for us to meet that challenge with new thinking and find solutions that we will use again in the future,” he says.