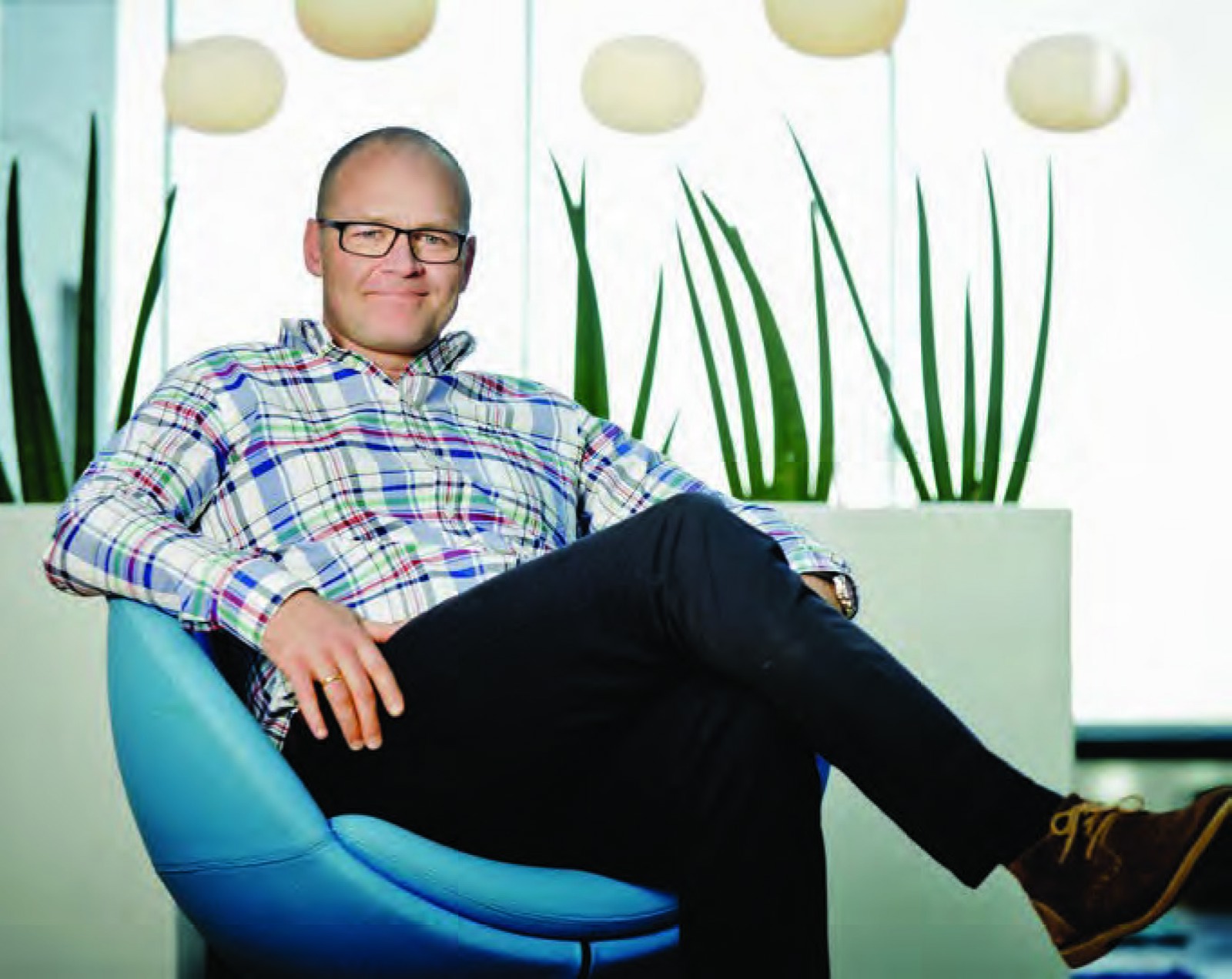
Leveraging LNG expertise
“From liquefaction plants, and coastal regasification import terminals to specialist tankers and mega floating production units, the LNG market and activities are humming” - Knut Ivar Dybdal, General Manager, Kongsberg Maritime LNG.
-
Text:Kongsberg Maritime Communication
-
Gunvor Hatling MidtbøVice President, Communications
LNG is one of the fastest growing energy markets globally. The number and scale of LNG projects proposed or under construction will double global production capacity. The International Energy Agency estimates more than $250 billion of new investment, in all parts of the LNG chain, will be required to meet demand until 2030.
“From liquefaction plants, and coastal regasification import terminals to specialist tankers and mega floating production units, the LNG market and activities are humming,“ says Knut Ivar Dybdal, General Manager of KM’s LNG section.
In the last five years, the volume of LNG available on the market has jumped 50 percent, three times faster than the overall growth of world gas production. LNG supply is expected to grow 4.4% p.a. to 2030, double as fast as total global gas production (2.1% p.a.). Europe and non-OECD Asia, particularly China and India, will lead demand growth securing major percentages of the global LNG increment. In 2010, the Asia-Pacific region consumed 60 percent of the world’s LNG, consuming 135.1 MMtpa of LNG.
Pushing the LNG carrier fleet to 360 ships, up from 195 ships end 2005, an average of 35 new LNG carriers have entered the market each year from 2006 to 2010. The combined capacity of the 2010 fleet totaled 53 million cubic metres.
“LNG continues to grow despite global challenges. We see an increasing demand for alternative uses of LNG ships, including floating regasification and/or LNG storage vessels. There are a growing number of private and national projects for floating liquefaction technology and vessels are getting more advanced and bigger, reflected by the growing Q-Flex (210,000-217,000 cm each) and 14 Q-Max (>260,000 cm) fleet,” says Dybdal.
Escalating natural gas prices and widespread competency in the LNG value chain today makes transporting LNG over long distance economically feasible. And with Australia and Africa becoming major LNG providers in the future, natural gas is evolving from a regional to a global market.
LNG – IT’S ALL ABOUT EXPERTISE
KM’s LNG activities took flight in 2000 after installing a fully integrated automation system (IAS) onboard the 87,600 cm LNG, Høegh Galleon. In 2001, KM delivered similar IAS systems to seven LNG tankers built by the three largest shipyards in Korea (Hyundai, Samsung and Daewoo). Two years later, KM landed control system contracts for four LNG tankers built at Mitsubishi Heavy Industries. The vessels, two owned by Hoegh and two by K-Line have been carrying LNG from the Snøhvit field to the USA, Spain and France since 2006. Working collaboratively with LNG players growing and seeing a rising demand for truly “mission critical” technology and vessel requirements, KM developed its own center of LNG excellence in 2005. Today, it has a highly experienced team of LNG specialists in Norway and Korea.
“Our LNG order book grew extensively. Splitting our focus areas into a dedicated LNG division, able to fully follow a specific market and refine breakthrough technology and concepts, has significantly enhanced KM’s ability to meet and exceed its LNG growth and goals. Without a doubt, KM LNG drives valuable results for the company and the client,” says Dybdal.
KM technology highly applicable to LNG includes Integrated Automation System, Custody Transfer System, Emergency Shutdown System, Engine Control Fire and Gas, and Integrated Bridge System. Additionally, KM has provided Dynamic Positioning for Hoegh’s SRV vessels.
KM technology grants effective LNG operation, says Dybdal, pinpointing KM’s custody transfer system.
”CTS, like all of KM’s LNG applications, is state-of-the- art technology,” optimized for LNG operation. CTS monitors LNG volumes at export and import terminals. How much did the ship fill, how much did she export, are extremely important commercial aspects for the owner and charter,” says Dybdal.
KM’s state-of-the-art, fully integrated automation system technology – a world standard for many vessels – and a number of prestigious, innovative LNG projects from 2000 – 2006, gave KM a world-recognized LNG expertise edge.
But LNG innovation is often short lived, that is, often changing and advancing with each LNG newbuilding.
“The dynamic world of LNG technology demands continual hightech innovation – things are changing all the time,” says Dybdal.
The challenge facing LNG players will be to pinpoint long-term trends and select import markets. In addition, owners and operators must continually raise the bar in technical LNG expertise and operational efficiency for specialized vessels such as FSRU’s, FLNG, LNG power plant vessels etc.”
GLOBAL COLLABORATION
Less than a decade ago, KM’s LNG section managed most activities from engineering and commissioning to gas trials from Norway. But this has changed. Today, development of new solutions and initial engineering are done in Norway. Assembly, installation and commissioning are done mainly by our colleagues in KM Korea, and further also in KM China. There is a very good cooperation within the project teams across country borders and long distances.
The technology teams are under constant pressure to continuously innovate with greater efficiency. LNG’s fast paced business environment requires KM to explore the use of external sources for technology to augment in-house R&D.
“Typically we utilize another Kongsberg product, Dynamic Simulator, to simulate the live process for proofing control system solutions and pre-tune the functions before commissioning. We keep core technology within our company and rely heavily on global competence from our sister companies in Korea, Singapore and China. To achieve the full LNG integration picture, we collaborate with the best to create the best,” said Dybdal.
In 1999-2000, KM developed its automatic boiler control system together with Kawasaki and Mitsubishi and compressor control with Cryostar. Later together with Cryostar, Samsung and DSME, KM developed its dual fuel gas management and vapor handling system. And reliquefaction plant to the Q-Flex fleet was developed together with Hamworthy Gas Systems.
To keep abreast the latest regasification unit development within FRSU, KM teamed up with world-leading LNG operator, Golar, and Hamworthy to create a total FSRU control system and process control philosophy.
Generally located near the LNG consumer site or power plants, FSRUs are dependent on a systematic level of control hierarchy, functional segregation and automatic integration. The control and safety system is usually composed of normal process control system, interlock and shutdown system, fire and gas system, and emergency shutdown (ESD) system.
“By drawing on each other’s strengths we have developed the most competitive LNG systems in the world. No one can deliver the full LNG picture like us. We are responsible for the whole package and will continue to develop new technology within the company and with chosen partners,” states Dybdal.
According to Dybdal experiences gained from LNG and FPSO are important foundations for delivering state of the art technical solutions to vessels like FSRUs.
“When a an owner calls on us, they know that we have the history, the competence and the ability, to ensure that new LNG concepts and systems are quality configured, designed for reliable, robust and safe operation,” said Dybdal.
NEW TECHNOLOGY IN THE PIPELINE
Projects, projects and projects. More projects enhance KM’s competitive edge and link up with leading LNG owners and suppliers in the development of new systems.
“Today, KM is collaborating with world-class LNG players to design better systems and equipment for superior LNG operation. This cooperation gives us unique market competence and strong competitive advantage ,” says Dybdal.
Presently, KM is further developing regasification plant technology with Hamworthy Oil and Gas Systems in Oslo, Norway, and is investigating new technology on how to convert two stroke ship engines into MEGI ( Main Engine Gas Injection).
Additionally, the company is developing tailor-made control systems for small to medium FLNGs and power plants to be ready when this side of the business kicks off.
“KM takes full responsibility for system interface and our team of LNG engineer experts are continually pushing our innovation, concepts and solutions,” says Dybdal.