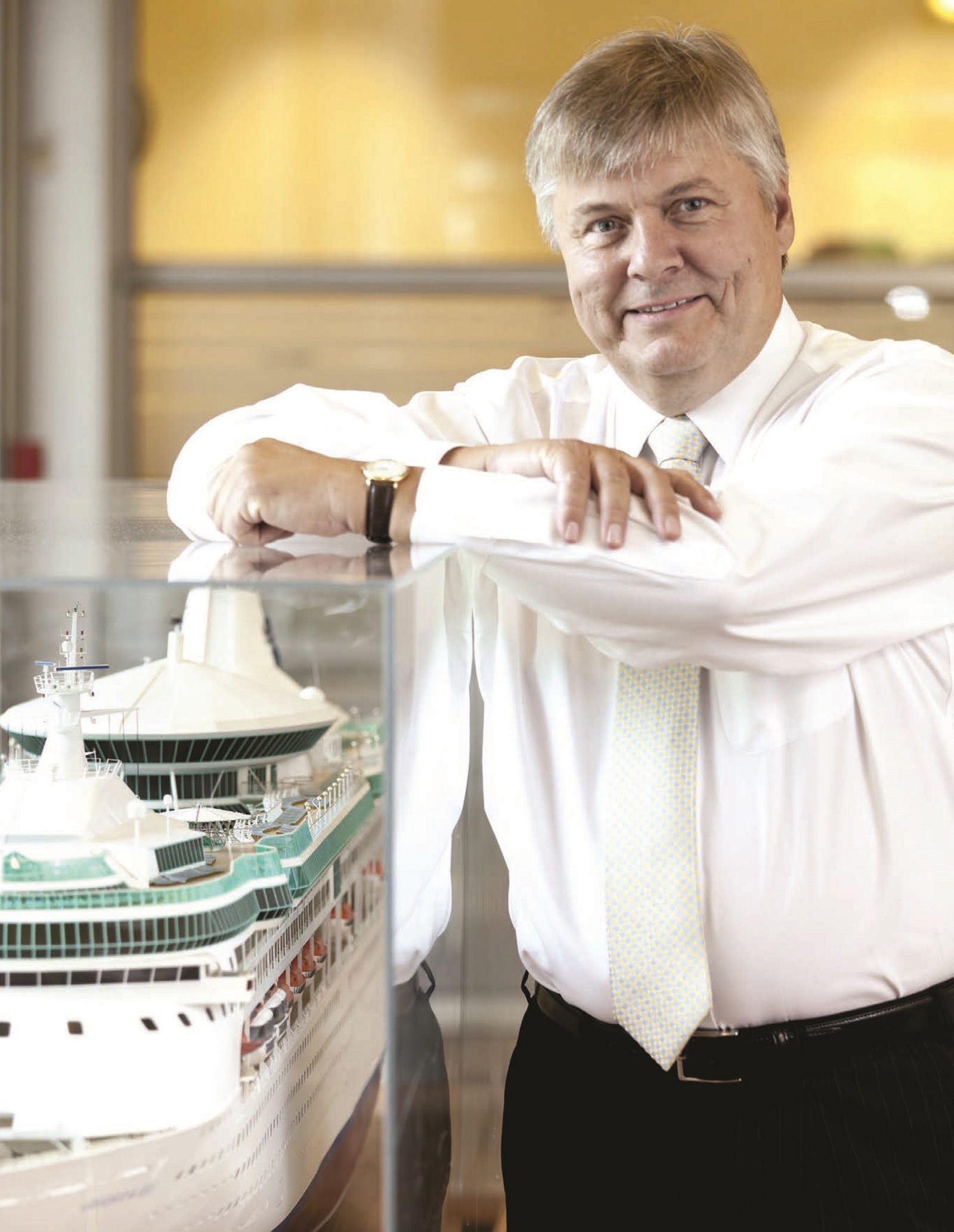
The shipping industry has long been criticised for failing to work together to address common challenges. But with the rising cost of bunkering and new international regulations coming into force, all that might be changing.
-
Text:Kongsberg Maritime Communication
-
Gunvor Hatling MidtbøVice President, Communications
The rising cost of energy and increased concerns about the environment have resulted in significant changes in the industry. In July 2011, the IMO introduced a new chapter 4 to Annex VI on Regulations on energy efficiency for ships (EEDI). The regulations apply to all ships of 400 gt and above and will enter into force in January 2013. At the same time, regulatory bodies in different states are working to introduce Emission Control Areas (ECAs). At present, sulphur emissions control areas (SECAs) are in effect in the Nordic region and the Baltic Sea and ECAs will be established in the English Channel, North America and some islands in the Caribbean. And earlier this year, the EU published a consultation document which considered a number of options for curbing emissions, which may take the form of a market-based mechanism that would apply to ships’ emissions in Eurozone waters or a “compensation fund” that would require owners to make payments to offset damages caused by carbon emissions.
MARKET FORCES
But according to Henrik O. Madsen, CEO of DNV Group (Det Norske Veritas) market forces have also played a role. “Bunkering prices have tripled over the last three years and while oil prices remain volatile, most analysts agree that prices will continue to rise for some time,” he says. “For owners, these prices represent a serious business risk. Between new and existing regulations on emissions and bunker costs, the industry is looking for solutions.”
Madsen notes that as a class society, DNV works with owners, suppliers and regulators on a broad range of issues related to climate change and fuel efficiency. “At present, DNV is participating in more than 30 Joint Industry Projects with various maritime industry stakeholders, is active in a number of other smaller scale projects in cooperation with universities and technical institutes and regularly consults with regulators and other class societies,” he says. “We are also working with other industries, such as aviation and auto manufacturing, on a number of safety and logistics initiatives.”
MANAGING BUSINESS RISK
While DNV’s primary goal is safety risk management, Madsen is quick to note that DNV also offers services related to managing business risk. “The scope of our technical expertise and close cooperation with industry players has allowed us to see these issues from a broader perspective,” he says. “And after working in cooperation with a number of suppliers, owners and regulators, we have demonstrated that the industry can achieve common goals by working together.”
Owners developing new vessel concepts are faced with a broad range of options to improving energy performance, ranging from innovative hull forms to new types of propellers, rudders, thrusters, propulsion and automation systems, to name a few. Madsen acknowledges that all these components can impact emissions and fuel costs, but says it is how they work together (or don’t) that makes a big difference. “The point is, there is no quick fix or single technology that can improve fuel efficiency,” says Madsen. “Only by utilising different technologies and integrating them properly owners can improve fuel efficiency and reduce emissions. And that requires cooperation.” Madsen says that DNV’s in-house expertise in propulsion, noise and vibration, hydrodynamics and machinery among other specialised services, allows the organisation to bring some fresh ideas to the table during the design phase.
Indeed, DNV’s collaboration with different stakeholders helped inspire a unique development initiative. Two years ago, DNV began an innovation programme to develop concept vessels for different segments. The purpose of the programme was to show how the industry could make use of existing technologies to reduce fuel costs and lower emissions. While some these concept vessels include well-publicised innovations, such as LNG-fuelled engines, it was the combination of many different components that made the difference. “We saw that by adopting a number of innovative solutions and integrating them properly, owners could both comply with emerging regulations and achieve significant long-term savings.”
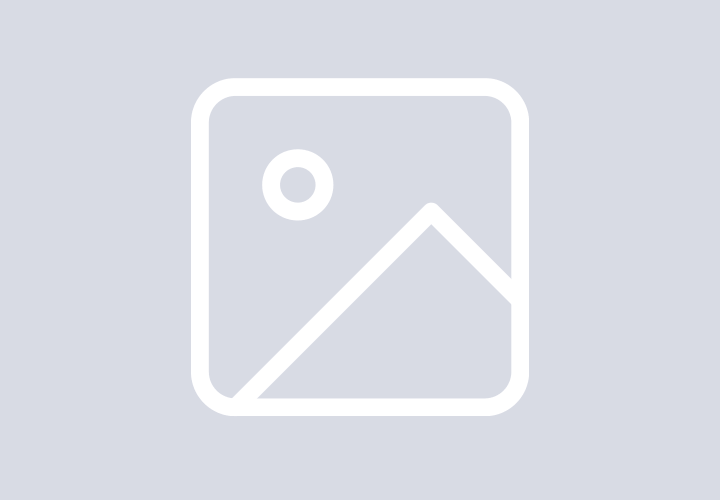
Ship shape concept: DNV’s Triality VLCC offers an array of innovations, including eliminating the need for ballast water.
INTEGRATING TECHNOLOGIES
To ensure a practical result, the DNV concept vessels were developed for typical trades and involved significant input from suppliers, shipyards and owners. For example, Quantum, DNV’s container ship concept is powered by four dual-fuel engines providing a redundant machinery system with flexible power generation over a variable speed range. The broad beam of the vessel (42.5m at waterline) improves stability and practically eliminates the need for ballast. With the WideDeck solution (49m at deck level) container capacity is improved without increasing the fuel consumption. A twelve-metre draft allows the vessel to trade in shallow waters, including river ports, and the unique shape of the Quantum’s bow helps reduce wind resistance, resulting in further fuel savings. In addition, the hull design specifications, including the use of new, lightweight composite structures utilising plastic laminates, reduce the vessel’s weight by an estimated 1,000 tonnes.
A NEW APPROACH TO VLCCS AND VLOCS
Triality, DNV’s concept VLCC, has two high-pressure dual-fuel slow speed main engines fuelled by LNG, with marine gas oil as pilot fuel. Its V-shaped hull form and cargo tank arrangements completely eliminate the need for ballast water in the VLCC version. The new hull shape results in a reduced wetted surface on a round trip and has a lower block coefficient and thus a more energy efficient hull. The Triality VLCC can collect and liquefy more than 500 tons of cargo vapours during one single round trip. These liquefied petroleum gases will then be stored in deck tanks and up to half will be used as fuel for the boilers during cargo discharge, while the rest can be returned to the cargo tanks or delivered to shore during oil cargo discharge.
Ecore, DNV’s VLOC concept vessel, represents a step change in bulk carriers. Powered by two-stroke dual fuel ME-GI engines, this concept features a more ballast-friendly hull shape, a large centre cargo hold that was developed to minimise the need for ballast, enables more efficient cargo handling and space for LNG tanks to be stored below the main deck.
Madsen says that the DNV concept teams also consulted with a broad range of suppliers and equipment manufacturers to include smaller innovations, from new propeller designs to rudder profiles, waste heat recovery systems to coatings solutions. “Alone, these elements may not cut fuel costs significantly, but by integrating a number of technologies and designs, these small changes add up to real savings.”
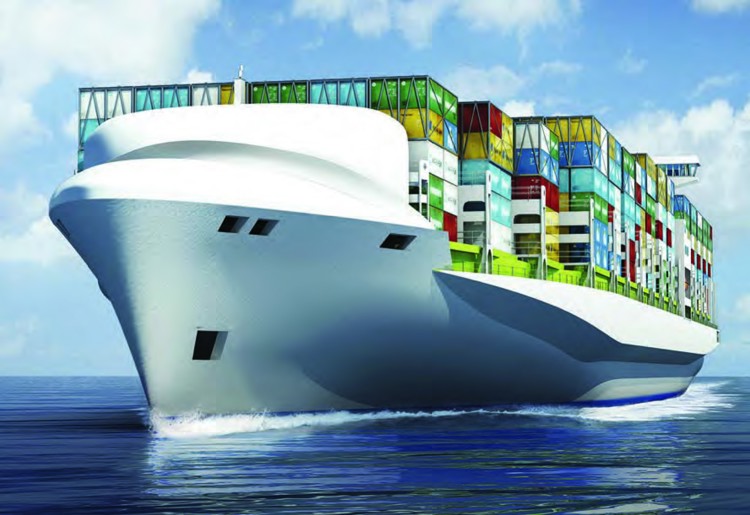
FROM CONCEPT TO REALITY
While DNV does not expect these concept vessels will be built as designed, Madsen notes that some elements are already being adopted by the industry. “DNV has worked closely with Oshima Shipbuilding Co., Ltd. on a joint programme to develop the ECO-Ship 2020, a concept design for an open hatch bulk carrier,” he says. “And we have worked closely with Man Diesel & Turbo to further develop the ME GI engine for the Quantum 9000 concept vessel.”
DNV has cooperated with Kongsberg Maritime (and other industry players) on a number of projects over the years, such as a research project on Arctic operations and technology and an initiative to develop improved methods for qualification of technology for power and energy management control and DP systems. The two organisations also participated (with others) in a JIP in 2007 organized by the Maritime Research Institute Netherlands to develop Service Performance Analysis, (SPA) aimed at optimizing ships’ fuel efficiency. And earlier this year, DNV, Kongsberg Maritime and IBM announced plans to develop a real time environmental monitoring system for Statoil’s Research and Development Center in Trondheim.
SHARING KNOWLEDGE
“As a leading supplier to the maritime industry, Kongsberg Maritime understands the benefits of cooperation and has made some real contributions to safety and fuel efficiency over the years,” says Madsen. “By working on a project structured to share knowledge they not only add genuine value, they gain critical data they can use to strengthen their business.”
While Madsen acknowledges the industry still has a long way to go, he argues that the challenges faced by the industry at present represent a genuine opportunity for change. “In the end, fuel savings and emissions control is as much about attitude than it is about technology,” he says. “And for the first time, fuel efficiency and harmful emissions are closely linked to business risk – a strong incentive for industry stakeholders to recognise the benefits of collaboration. We welcome this development and stand ready to do what we can to bring the industry together.”