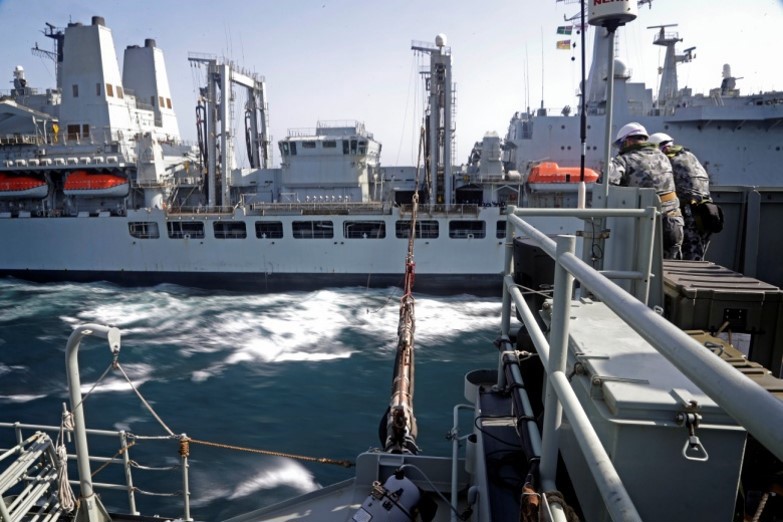
Replenishment at Sea that’s Faster, Safer, and More Reliable
Apart from providing a stable platform for force projection and defence, one of the most important tasks of any Naval vessel is Replenishment At Sea (RAS). RAS is a force multiplier that extends the range and time at sea of both surface combatants and amphibious vessels, especially during multi role operations, when vessels go through munitions, food, and fuel at exponentially faster rates. All modern Navies require RAS capability to operate in these challenging and extreme conditions.
RAS is also one of the most dangerous tasks that Naval vessels perform. Ships in a resupply configuration are restricted in their ability to manoeuvre and will have to rely on others within the task group to provide operational defence whilst resupply operations are undertaken. Station keeping between large naval ships during abeam replenishment is a safety critical operation due to repulsion and attraction forces on the hulls caused by pressure wave interaction between the ships as they sail in close proximity. During this period, they are particularly vulnerable, so operational efficiency and equipment availability are critical.
Personnel safety is also a major consideration, as RAS Team members will be operating pressurised equipment in an unforgiving environment. Traditional hydraulic RAS equipment is under high pressure during operations and that risks leaks and spills during mission critical evolutions.
Kongsberg Maritime has developed the engineering and design basis behind electrical RAS equipment.
Electrical RAS systems can also be deployed quickly after long periods of inactivity and are significantly more reliable than hydraulic systems when installed in an open deck marine environment. They require less maintenance and overhaul periods in service, which also reduces overall lifetime costs of the system. The marine environmental risk of volume oil spillage is also eliminated.
One of the greatest examples of long-range naval operations – and the challenges therein – came during the 1982 Falkland Conflict, in which the Royal Navy went into action over 7,000 nautical miles from home. The lessons learned from that deployment, including the importance of quick and effective RAS operations, were behind the initial designs for Kongsberg Maritime’s electrically operated RAS equipment.
Since then, Kongsberg Maritime has continued to pioneer and develop the use of electric motors powering the winches and stays on a RAS system. Today, Kongsberg is the leading supplier of electrically operated RAS systems because it is the proven way to get better RAS results over the lifetime of a resupply vessel.
Kongsberg Maritime continues to develop the technology and capacity of its RAS systems, with a focus on making sure the maximum amount of supply gets to warships in the minimum amount of time, while maintaining a high level of safety, reliability, and system integrity.
A dedicated team of 50 people work exclusively on RAS equipment and design from our Gateshead facility in the UK, whilst providing close support for our customers. Over the past two years, Kongsberg has invested heavily in its RAS department, which has grown over 30% in size and resources in that time.
Those investments and developments yield huge advantages for RAS operators:
- A Royal Navy training facility at HMS Raleigh has been installed with Kongsberg Maritime Heavy RAS equipment, which can transfer loads of up to six tonnes at 25 loads per hour. The Royal Navy’s Queen Elizabeth Class carriers are already equipped with Kongsberg Maritime’s Heavy RAS receiving equipment.
- Receiving Ship’ equipment can be enclosed with a folding door and integrated into the ship’s superstructure. This protects the equipment from extreme weather and preserves the radar cross section reflection stealth characteristics of the vessel.
- Kongsberg Maritime’s RAS liquid system can deliver up to 1000 cubic metres of fuel per hour; 2000 if the resupplied vessel is long enough to have two delivery stations.
- Kongsberg Maritime has also developed special winches for the load-bearing line that generate additional electricity during RAS operations. That electricity can be used to help power operations or support the hotel load.
Navies around the world are expanding quickly. Kongsberg Maritime has already installed electrically operated RAS systems for the Royal Navy in the UK, as well as other global navies. Interoperability is a key component in future force projection. NATO Navies are adopting systems standards to allow supply vessels from one Navy to replenish vessels from another. Kongsberg is already helping one major European Navy switch from traditional, hydraulic RAS systems to electrical systems.
More navies are emphasising the need for long-range activity with a global reach into remote geographical zones including polar regions, for everything from force projection to international disaster relief. That puts more emphasis on the need for safer, quicker, effective replenishment at sea, often conducted in rough conditions. A faster, quieter, safer, and more reliable electric RAS operation reduces the risks and maximises the chances of a successful deployment.