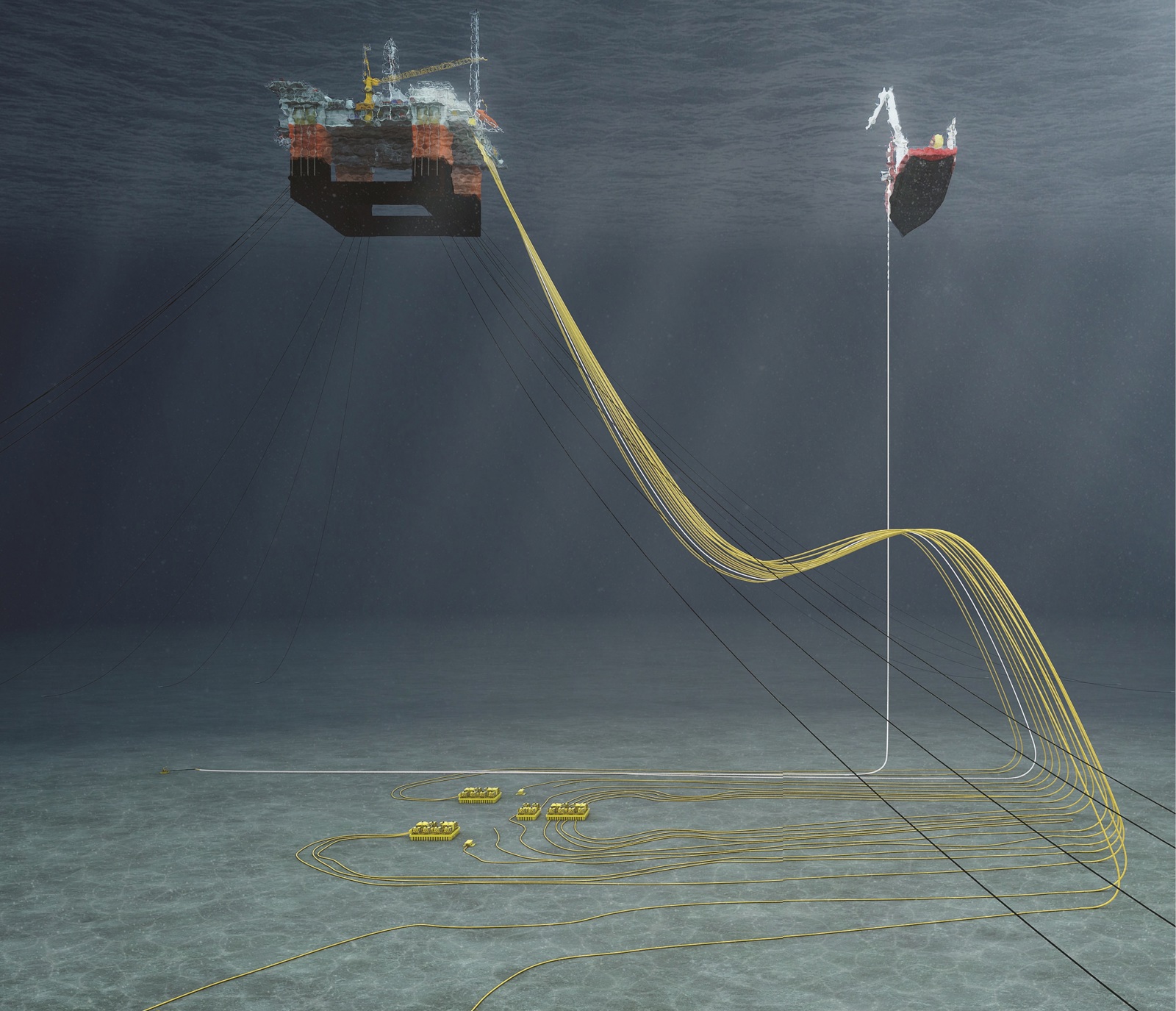
Positioned for subsea success
When Statoil needed to install new rig seabed risers on the semi-submersible production and drilling platform, Visund, it turned to EMAS AMC. This should be no surprise, considering it manages one of the largest and most advanced subsea installation construction vessels in the world.
-
Text:Kongsberg Maritime Communication
-
Gunvor Hatling MidtbøVice President, Communications
EMAS AMC is part of EMAS, a leading, full-field contracting group providing specialised marine support services, subsea construction and offshore installation, floating production, fabrication and well services to the offshore energy sector. Its modern fleet comprises over 65 marine support and offshore construction vessels, supported by over 5,000 employees across five continents.
EMAS AMC is the division in EMAS which delivers subsea construction and marine services to the offshore petroleum and energy industry.
A BESPOKE VESSEL
A recent addition to the EMAS fleet is the Lewek Connector, which is one of the largest and most high-tech, subsea installation and construction vessels in the world. With two offshore cranes with a capacity of 400 tons and 50/100 tons and with the ability to reach down to 3000 metres, Lewek Connector is specially designed for deepwater construction.
Øystein Fyrvik, Survey Manager, Operations, at EMAS AMC explains that for the Lewek Connector EMAS AMC charged Kongsberg Maritime with supplying both underwater and dynamic positioning (DP) systems - equipment that is integral to the effective operation of the Lewek Connector. He said: “The vessel is equipped with the latest DP3 vessel technology, which provides great stability in offshore operations, and allows us to carry out installation and construction work near offshore installations and in harsh weather conditions such as that found on the Norwegian Continental Shelf (NCS).”
KONGSBERG’s DP system is operating in conjunction with cNODE® transponders for underwater acoustic positioning and data links. They have more than 100 channels available and can all be positioned using HiPAP® underwater positioning systems. The Hi- PAP® technology consists of the world’s most successful underwater positioning systems, developed for use in deepwater and in accurate seabed survey applications. As a result of the latest developments of HiPAP® and cNODE® products, the onboard HiPAP® system can be used in the operation of high accuracy positioning tasks related to subsea positioning. By use of a Long Base Line (LBL) transponder array at the seabed, the remotely operated vehicle (ROV) is equipped with a KONGSBERG cPAP®, and can position itself within a few centimetres accuracy.
Fyrvik continued: “After delivery of the Lewek Connector from the yard in 2012 it was decided to upgrade the HIPAP system to the highest levels of accuracy for underwater survey purposes. All sensors were re-calibrated and the latest development of hydro acous- tic software was implemented. Today the HiPAP® system acquires a global position of <0.2 percent of water depth – a figure which is close to the “white noise” of hydroacoustics, and a very impressive underwater positioning accuracy for Lewek Connector.
THE VISUND PROJECT
Once fully operational, one of the first projects undertaken by the Lewek Connector was the replacement of flexible risers on the Visund semi-submersible rig. The platform itself is located directly above the completed subsea wells, operating in a water depth of 335m.
An essential element of the Visund riser replacement project is the use of a Schilling HD ROV. It is at this point that Kongsberg Maritime’s technology comes into its own. The ROV acts as the eyes of the operation as the 900-metre long, 30 centimetre diameter flexible risers are both recovered and installed in-between neighbouring risers a few metres apart, thus precise position is crucial. EMAS is among the first operators to use KONGSBERG’s new cNODE® and cPAP® technology.
Fyrvik describes the benefits of working with KONGSBERG systems. “Using the HiPAP and DP technology, we are able to perform an installation which is extremely demanding for both vessel positioning on the surface and product positioning at the seabed. On this riser replacement project, the vessel is working in between risers and anchor lines with a position envelope of +/-1m, and at the seabed, 320m down, the riser is installed within a 1m target area. To achieve this, the vessel’s DP system is linked to the survey and navigation system which continuously monitors the surface position of the platform and vessel, as well as the subsea position of several anchor lines, risers, ROVs and crane wires.”
He continued: “To install flexible risers over 300 metres below the surface to within a metre is an incredibly complex task. You have vessel motions, several hundred metres of flexible riser product and a great deal of hardware on the seabed that can get in the way of the operation.”
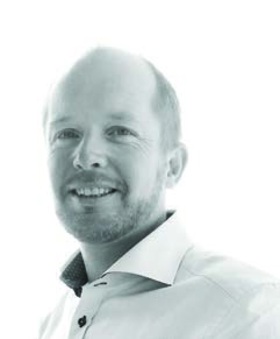
“To position riser cables over 300 metres below the surface to within a metre is an incredibly complex task” - Øystein Fyrvik, Survey Manager, Operations, EMAS AMC
The Lewek Connector has proven to be a highly efficient vessel for such demanding operations. This vessel is one of the world’s most advanced and flexible subsea construction vessels, and the largest. No other construction vessel can load as much product as the Lewek Connector: some 9,000 tonnes. The vessel also has two cranes with capacities of 400 tonnes and 50/100 tonnes respectively, which can operate at depths of up to 3,000 metres. Furthermore, the vessel is fitted with both a Vertical Laying System (150 tonnes) and a Horizontal Laying System (70 tonnes).
The Lewek Connector is equipped for laying products from the side of the vessel. Combined with very good movement characteristics, this allows the Lewek Connector to lay cables in tougher weather conditions than competing vessels. This, in combination with it being a highly stable vessel, having a state-of-the-art DP and positioning system and experienced on-board crew, ensures both efficient and safe offshore marine operations.
Jan Erik Faugstadmo, Vice President, Underwater Navigation, at KONGSBERG, added: “We worked particularly diligently to ensure the effectiveness of the transponders using a Multi User Long Base Line positioning system. The use of this technology is increasingly important due to the amount of equipment now being placed on the seabed. At the same time, several vessels and ROVs can position themselves using the same seabed transponder array, reducing costs and simplifying operations.”
The Lewek Connector always operates at a safe distance from the platform where environmental conditions such as wind, current and waves are taken into account. However, due to the efficacy of managing the positioning and movement of the vessel, this distance has in some cases been reduced to as little as 12 metres.
This is an example where the ultra-modern installation and construction vessel, Lewek Connector benefits from superior manoeuvrability and excellent station-keeping capabilities.
A CHALLENGING PROJECT
Of the association with KONGSBERG, Fyrvik has nothing but praise, though the relationship was a challenging one, particularly in the early phase. “To begin with, we were finding that Long Base Line positioning at Visund was not performing as expected. It appears there is a tidal wave of cold water along the seabed that impacts the acoustic LBL calibration. But the input of KONGSBERG’s soft- ware engineers was invaluable as they worked tirelessly to develop software to compensate for this phenomenon, and the end-result is a stable LBL system which positions the ROVs at the seabed within 5cm relative accuracy. “
He continued: “The process was also significantly aided by KONGSBERG appointing a single contact person to manage our account on a daily basis. This means that our manager has in-depth understanding of the technical issues relating to our vessel and the project.”
A further advantage of EMAS AMC partnering with KONGSBERG is that KONGSBERG was and is able to undertake total systems integration, aided by technicians with comprehensive hydro acoustic knowledge. This makes projects much more cost-effective and reduces timelines. Additionally, Kongsberg Maritime is able to equip vessels with equipment from multiple suppliers, providing customers with significant flexibility in meeting their project demands.
As a marine operations specialist engineer and Survey Manager in EMAS AMC, Fyrvik is part of the EMAS AMC operational team and in daily contact with the Lewek Connector personnel on-board the vessel. He also tries to spend some of his time on-site to understand the issues involved in the job. “It is a very innovative environment and one that changes quickly, so it is important to be in-situ to understand the changes taking place.”
He concluded: “Each job has its own challenges which need innovative solutions and good planning. A project is never the same in theory as in practice, but on the Visund project the Lewek Connector – aided by the systems from KONGSBERG – performed well in testing and now in operation. The Lewek Connector will now move on to work at Njord and I’ll soon move on to working with nearshore activities and challenges for cable installation from Troll platform to Kollsnes, part of the Troll gas development. I hope and expect just as exiting and successful a project!”