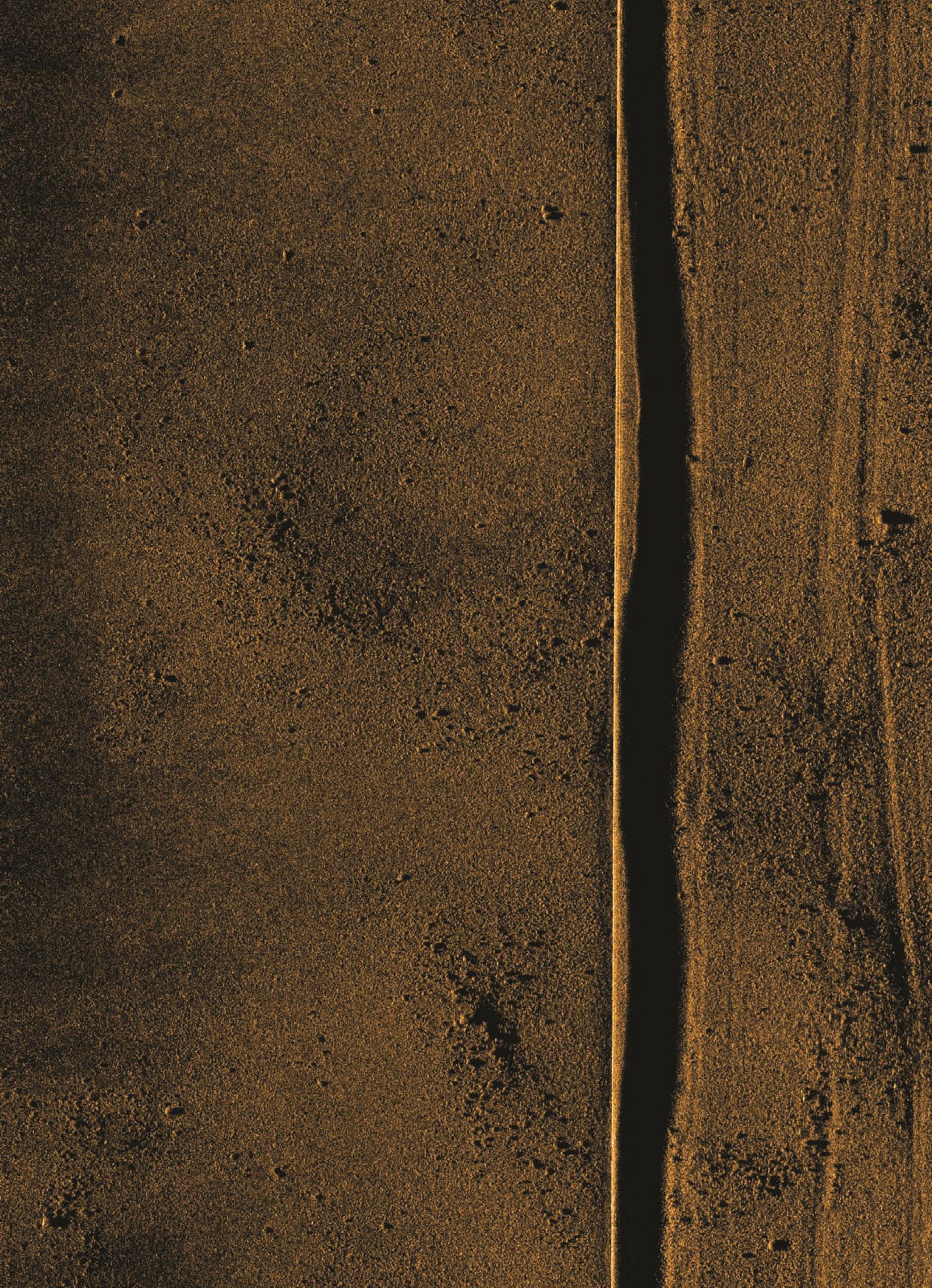
Subsea pipelines are critical infrastructure components for the oil and gas industry. They are also expensive. So expensive in fact, that there is often little or no redundancy available should things go wrong, so inspection and maintenance are vital ingredients to ensure that oil and gas continues to flow.
-
Text:Kongsberg Maritime Communication
-
Gunvor Hatling MidtbøVice President, Communications
Any disruption to oil and gas flow could have formidable financial and social repercussions, not to mention the environmental consequences of a possible leakage. To ensure a high degree of integrity, subsea pipelines are therefore designed and built to a very high standard, but this must be complemented by rigorous and extensive inspection programmes.
“The main threats to a pipeline differ with location and water depth,” explains Per Espen Hagen, the Senior Principal Engineer in charge of System Architecture at Kongsberg Maritime Subsea AUV department, whose job it is to understand the challenges of ensuring subsea pipelines continue to work.
“Natural phenomena such as hurricanes, seismic activity and sediment shift may be of vital concern in many parts of the world. In other areas, human activity such as bottom trawling or anchoring may pose the greatest risk to pipelines. Regardless of the local challenges, a robust, economic and efficient inspection regime is needed in order to maintain pipelines to a high standard.”
According to Hagen, the main objectives of an inspection programme vary with the threat scenario, but can typically include factors such as determination of burial, free span and buckling, as well as any kind of damage to the pipeline.
“In addition to the pipe itself, it is normally also of interest to gather data from its surroundings, to scan for debris and evidence of potentially damaging human activity. These diverse tasks are best solved by recording data with a variety of sensors, both acoustic and optical,” he adds.
GOING AUTONOMOUS
Today, external pipeline inspection is often performed with towed or Remotely Operated Vehicles (ROVs). For the past several years, however, Kongsberg Maritime has been developing a concept for pipeline inspection using the HUGIN autonomous underwater vehicle (AUV).
The primary advantage of using an AUV for this task is that it can operate at substantially higher speed – typically 4-5 knots, compared to 1-2 knots for a ROV. Secondly, AUVs can carry out their mission without being followed closely by a large surface vessel. Thirdly, the higher stability of AUVs means that they can effectively collect more advanced types of sensor data, such as Synthetic Aperture Sonar (SAS). The switch to using AUVs for pipeline inspection isn’t an easy one though.
“The AUV must autonomously perform many tasks that were previously carried out by the ROV operator. This includes actually detecting and tracking the pipeline from the sensor data, and positioning its sensors optimally relative to it. The technology exists though, and we have developed a solution that allows the autonomous, relatively high speed inspection of subsea pipeline,” says Hagen.
He is referring to a joint project with the Norwegian Defence Research Establishment (FFI), where Kongsberg Maritime has developed advanced algorithms for robust detection, tracking and following of underwater pipelines and cables using HUGIN. FFI leveraged 15 years of experience in sonar data analysis developed for other applications, such as automated target recognition (ATR) in mine countermeasure applications, as part of the project and trackers have been developed for side scan or SAS imagery, and for bathymetry.
This concept for multi-sensor AUV pipeline inspection has been field tested in various scenarios since 2009, with a full scale test of the complete system performed in the North Sea in July 2012.
“We see that acceptance is growing, and it is fair to assume that AUVs with this technology will be a major contributor in pipeline inspection in the future”
SUCCESSFUL TRIALS
The HUGIN AUV was mobilised on the ship M/V Icebeam, owned and operated by the Swedish survey company Marin Mätteknik (MMT). A portable HUGIN system, which comes in a 20 ft container (including the launch and recovery system) with a separate 10 ft operations container was used for the trial. The system also included a portable HiPAP system for acoustic positioning, a Seapath navigation system, acoustic, RF and satellite links, as well as all necessary maintenance equipment.
The complete system was mobilised on M/V Icebeam in a day, including HiPAP calibration at sea, which demonstrated high flexibility for commercial deployment in the future. Following mobilisation, the ship transited to the area of operations and a comprehensive four hour HUGIN test dive was executed. The AUV then performed two 13-hour dives over the next two days. After transit back to port, the entire system was demobilised in half a day.
The main sensor instrumentation for pipeline inspection with a HUGIN AUV is the HISAS 1030 interferometric SAS, the EM 2040 high-resolution multi-beam echo sounder, and the TileCam still image camera system, all of which were utilised during the sea trials.
Hagen describes the operations: “In the first survey mission, HUGIN tracked and followed the pipeline continuously with HISAS for almost seven hours, covering a 49 km section at 4 knots – twice as fast as an ROV, and without the need for an operator of course. HUGIN then turned around, and tracked the same pipeline section using an EM 2040 multibeam and TileCam continuously for around 4 ½ hours, covering a 30 km section at 3.8 knots. In this phase, the AUV operated at 3.5 metres above the seabed, and excellent camera images were collected.”
Various combinations of AUV speed, altitude and sensor settings were tested in order to optimise multibeam coverage and sounding density during the trial. The EM 2040 achieved ping rates exceeding 40 Hz, providing approximately 5 cm sounding spacing both alongtrack and across-track, which is more than enough definition for a high-resolution inspection. The stable environment on the AUV allows practically every single sounding to be used, facilitating DTM production at cell sizes of 10x10 cm or even smaller.
NEXT STEPS
Analysis shows that the concept will provide considerable cost and time savings compared to the traditional methods for pipeline inspection. One obstacle to the adoption of the technology is that while the data set collected is very rich and of excellent quality, it differs from the products gathered by ROV inspection, so changing the way the industry operates pipeline inspections will not happen overnight.
“We see that acceptance is growing, and it is fair to assume that AUVs with this technology will be a major contributor in pipeline inspection in the future. Furthermore, the concept can also be extended to other, similar forms of subsea infrastructure, such as cables, so we are confident that our work can enhance inspections in a number of subsea application areas.”