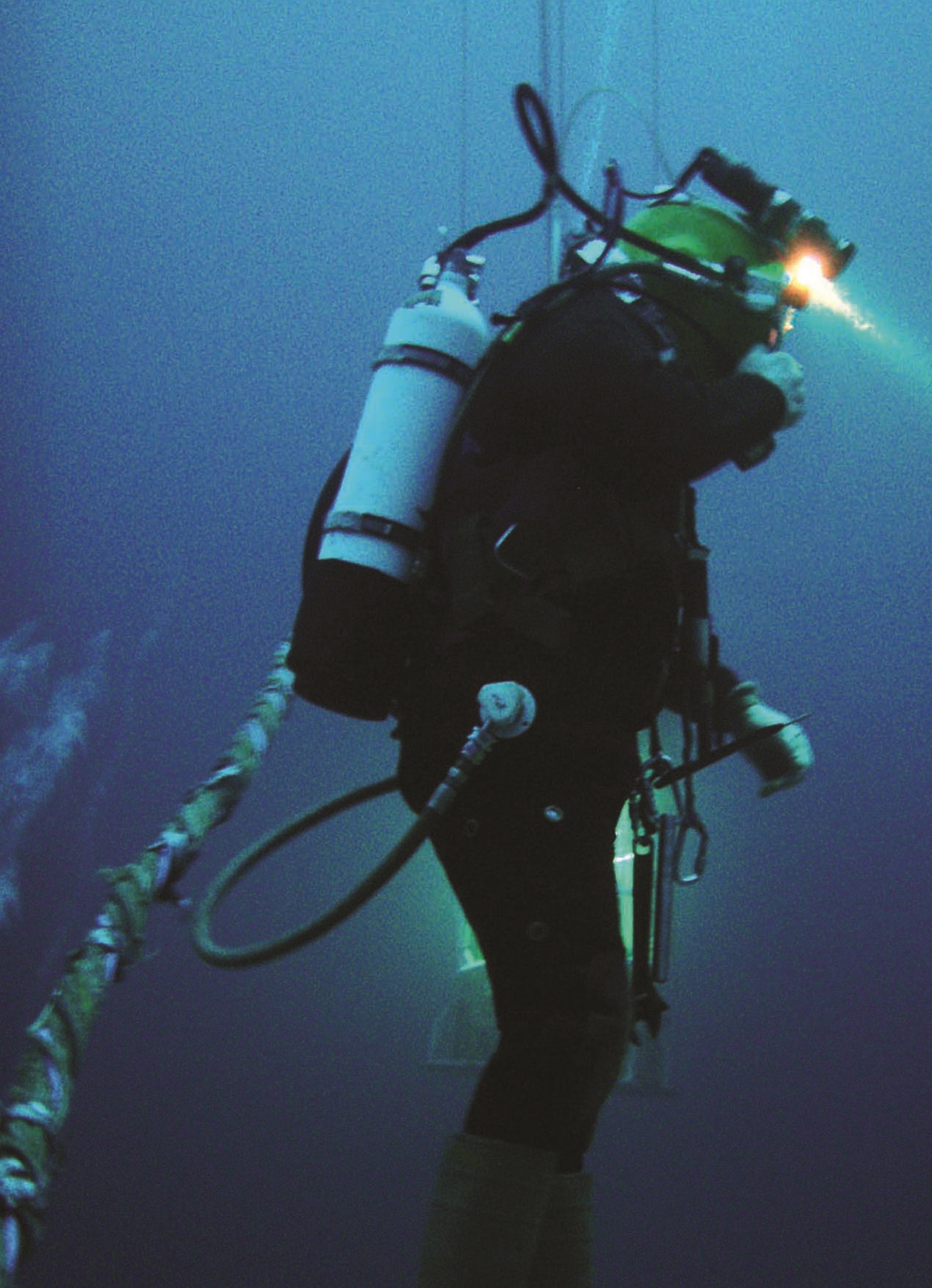
Evolving technologies have enabled the offshore industry to operate in ever-harsher environments, more remote locations and at greater depths. But for the elite saturation divers reliable technology isn’t just a benefit – it is matter of life and death.
-
Text:Kongsberg Maritime Communication
-
Gunvor Hatling MidtbøVice President, Communications
Today, there are about 60 purpose-built Diving Support Vessels (DSVs) in the world fleet, supporting about 3,000 commercial divers and crew working in subsea environments all over the globe. Many of these divers operate in shallow water, but those at the top of their profession are known as saturation divers, highly skilled personnel who can work at depths of up to 300 meters. While no part of the offshore industry tolerates downtime due to mechanical failure, for divers, systems reliability is matter of survival.
According to Sverre Gylseth, a former saturation diver who now works as a Principle Surveyor for Det Norske Veritas (DNV), commercial diving requires a level of trust in personnel and equipment that may only be familiar to astronauts, trapeze artists and tandem skydivers. “While most people think of sat divers as daredevils, most are very cautious – they have to be to function in such a dangerous workspace,” he says. “But there is only so much a diver can do to ensure his own safety – they have to rely on equipment and their dive support team for their survival – especially if something goes wrong.”
A RISKY PROFESSION
And things do go wrong. According to the US Center for Disease Control (the most recent study to include commercial diving was released in 1998), “sat diving” was the third most dangerous job (behind logging and fishing) for “occupational fatalities.” Commercial diving is an insular community, so accurate figures for annual diving fatalities are hard to come by, but they do occur with depressing regularity. However, new technologies are being introduced to manage risks. “Apart from the coffee maker, pretty much everything aboard a Dive Support Vessel has one purpose,” says Gylseth. “To deliver a man to a subsea pipeline or installation, and return him safely back to the surface.”
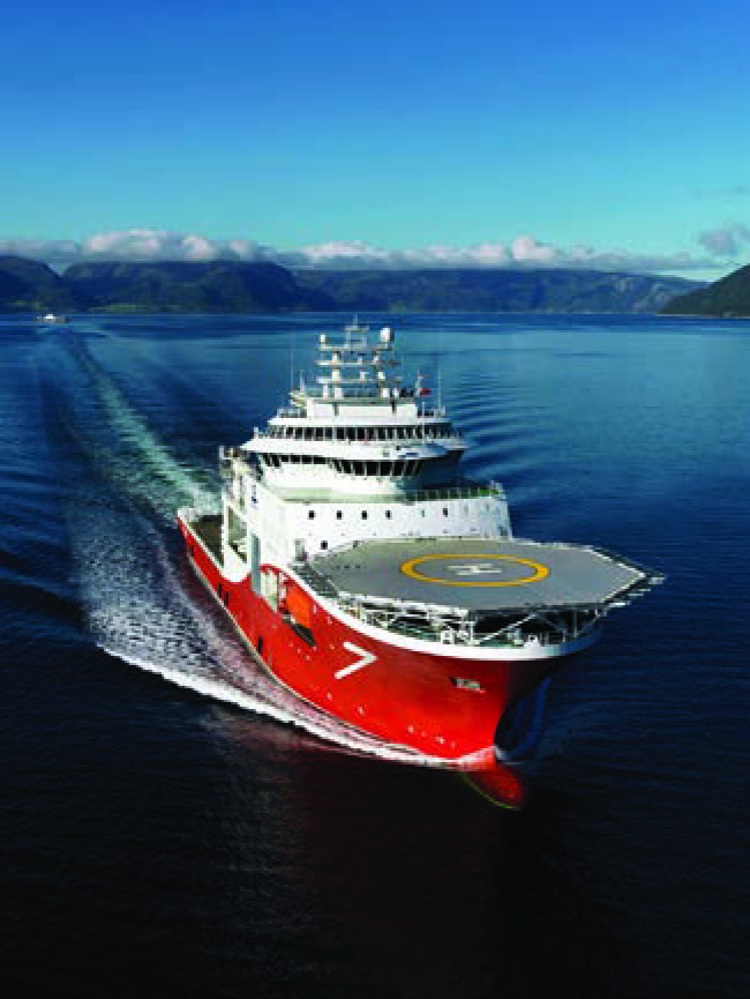
Unlike shallow water dives, preparations for deep sea diving begin in a “dive system” either installed into a DSV or mounted on a rig. A dive system looks a bit like a small space station and usually has four main compartments: living chambers, which resembles a berth of a submarine, small compartments that contain a toilet, a sink, and a showerhead, diving bell(s) and hyperbaric rescue chamber(s) – a capsule which has enough breathing mixture to last the crew for three (or more) days. Dive systems come in different sizes, with a capacity ranging from six to 24 divers.
UNDER PRESSURE
Once the divers enter the dive system, the inner environmental pressure is increased until it matches the pressure at the job’s working depth – this generally takes less than 24 hours. In addition, the breathing mixture inside the complex is also adjusted correspondingly – the deeper the job, the more helium will be added to the breathing mixture. “Helium is easier to breathe under pressure because of its low density and helps divers avoid nitrogen narcosis,” explains Gylseth. “Breathing nitrogen at depth is like being drunk, and represents a genuine occupational hazard.” Indeed, some divers refer to nitrogen narcosis as the “Martini Effect”, calculating that every ten meters of depth is the equivalent of drinking one martini.
MAN VS. MACHINE
Once pressurized, the divers can get to work. Two or three-man teams enter the diving bell, which is lowered to the work site on the seabed via a “moon pool” cut into the bottom of the DSV. The bell man stays in the diving bell while one or two divers swim to their worksite, which can be anything from subsea installation to risers and pipelines. While Gylseth notes that some of this work can be undertaken by Remote Operated Vehicles (ROVs), divers are necessary for more complex jobs. “So far, no technical solution has been developed that can compete with an experienced diver,” he says. “The ability of a diver to process information and utilise the dexterity of his hands cannot be easily replaced with a machine.”
Gylseth says that underwater working conditions are often very difficult. “Below 60 meters, there is no natural light, and despite dive suits insulated with warm water, it can get chilly,” he says. “Also, because sound is transmitted easily below the surface, the noise from engines and thrusters is very loud – a bit like working at a engine factory. With senses limited to sight and touch, it can be very disorientating.”
SEAFOOD
Currents can make navigating around complex structures difficult, especially since divers are tethered to the diving bell by a thick umbilical cable, which carries breathing gas, warm water and electronic systems and sensors. “In some ways, divers are a bit like astronauts performing a spacewalk, although astronauts don’t run into large fish with big teeth,” he says. “It’s hard enough to concentrate underwater as it is without having to worry about barracudas, 100 kilo groupers, wolf eels and manta rays that may linger around subsea structures.”
Gylseth adds that communications with the diving supervisor topside are complicated by the helium in the breathing gas. “Divers sound like Donald Duck, or like kids who have inhaled helium from balloons at a birthday party,” he says. “It may sound comical, but the risk of misunderstandings can result in mistakes. Some control panels are equipped with ‘Helium Speech Unscramblers’, a device that slows down the speed of the divers’ voices to improve coherency and thereby safety.”
WORKING IN SHIFTS
Dive crews can work without interruption in consecutive eight-hour shifts, making possible twenty-four hours of continuous work, with three different dive crews rotating into the bell from the dive system topside. Indeed, some of the larger, more advanced DSVs are now equipped with two diving bells, which can ferry divers to the worksite. A second dive bell also helps avoid downtime in the event of a system failure in the first bell, or can serve as a rescue bell if the first bell is compromised.
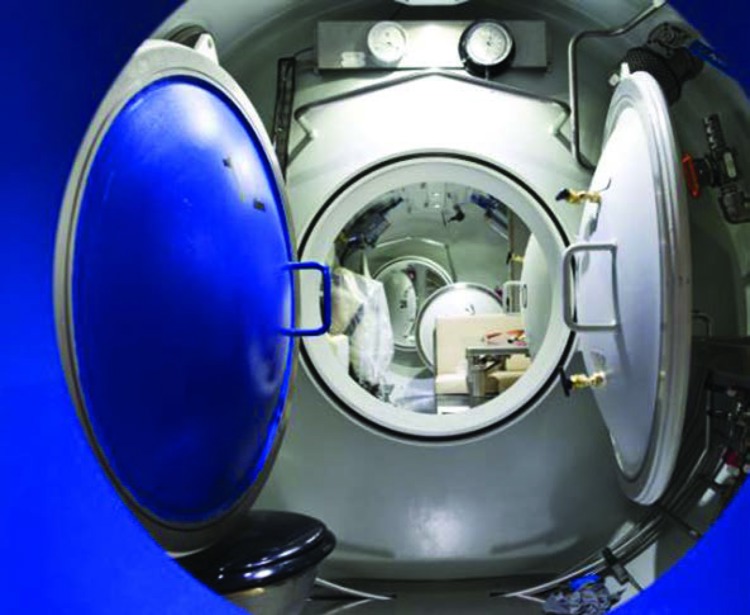
While divers rely on a broad range of systems aboard a DSV to get to and from work safely, ensuring the vessel remains in place (station-keeping) during dive operations is perhaps the most challenging. As a recognised pioneer in the development of DP systems, Kongsberg Maritime is a market leader in supplying DP systems to operators of DSVs. Unlike most offshore vessels, DSVs often operate in open water, without easily visible reference points that can be detected and processed by sensors that feed information into a Dynamic Positioning (DP) system. Furthermore, station-keeping for a DSV is further complicated when the bell is deployed.
According to Nils Albert Jenssen, Business Development Manager for Kongsberg Maritime, a deployed diving bell acts as a sea anchor, subjecting the vessel to subsea currents not detectable on the surface that can impact a vessel’s ability to stay in place. “In the world of dynamic positioning, the two greatest challenges for reliable station-keeping are deepwater drilling and DSVs,” he says. “However, while a system failure for a deepwater drill rig might result in downtime, a DP systems failure on a DSV could result in a fatality – there is little margin for error.”
“Apart from the coffee maker, pretty much everything aboard a Diving Support Vessel has one purpose. To deliver a man to a subsea pipeline or installation and return him safely back to the surface” - Sverre Gylseth Principle Surveyor, DNV
REDUNDANCY, REDUNDANCY!
Jenssen explains that a DP system on a Platform Supply Vessel (PSV) might typically rely on data provided by differential GPS satellite telemetry and another relative system, such as a laser-based reference system, which can be pointed at a fixed structure such as a rig or platform, to calculate relative distances. When combined with radar and sensors measuring wind, current and wave action, a PSV can retain its position within a few metres.
However, DP systems aboard DSVs rely on a number of additional sensors, such as hydro acoustic positioning systems with acoustic transponders placed on the seabed and taut wire systems. In addition, DSVs must be equipped to track the position of a deployed bell. “The more reference points the better,” says Jenssen. “For DSVs, the name of the game is redundancy.”
Indeed, DSVs are required by the authorities to be equipped with DP2 or DP3 systems. For DP2, class rules require built-in redundancy so that no single fault in an active system (such as generators, thrusters, switchboards, etc.) will cause the system to fail, but may occur after failure of a static component, such as cables, pipes, manual valves etc. The same rules apply to DP3, but the system must also be able to withstand fire or flood in any one compartment without the system failing, which means that also static components as mentioned above must be taken into account. “We recognise that commercial divers depend on Kongsberg DP systems for their survival, and continue to develop better, more reliable systems to ensure their safety.”
DIVERS IN DEMAND
In the meantime, there is more and more work for commercial divers. Global demand for oil and gas has encouraged energy companies to seek reservoirs in new areas, expand operation in existing fields and contract oilfield services companies to build, maintain and repair subsea infrastructure. At the same time, growth in offshore wind will create demand for new kinds of shallow water dive systems while more divers will be needed for subsea well decommissioning.
For Gylseth, the segment faces some challenges. “It’s a good time to be a commercial diver, but it remains a very specialised profession that takes years to master,” he says. “There is some concern that a new generation of divers, lured to the job by the promise of big pay checks and lots of vacation time, will lack adequate training.”
However Gylseth notes that in addition to investing in new training facilities, a number of different industry stakeholders are working together to minimise risk and improve safety. Indeed, DNV, Kongsberg Maritime, Statoil and Subsea 7 (a leading subsea oilfield services company) are working together in a Joint Industry Project to address issues unique to this specialised segment. “We are looking at how risk management tools, such as Environmental Regularity Numbers and Capability Plots, can be applied to the design, construction and safe operation of DSVs,” he says. “As an ex-diver myself, I am pleased that the industry has not only recognised the value of experienced divers, but is working together to prevent accidents. Commercial diving will always be dangerous, but it should never be fatal.”